Mitigating fire risks in CNC machining operations
By OEM Update Editorial December 21, 2023 1:55 pm IST
Investing in CNC milling, turning, or grinding centres offers exceptional productivity, but using flammable fluids and potential mechanical errors poses critical fire hazards within these industrial setups.
Investing in industrial CNC milling, turning, or grinding centres represents a smart business decision. CNC machines offer remarkable speed, precision, and consistency in part production, providing a competitive advantage in challenging economic conditions. However, despite their safety features, CNC machines are susceptible to fire.
Many CNC/EDM machines use oil-based metalworking fluids, coolants, and lubricants. These substances are flammable, with flash points ranging from 170° to 350° Celsius, and are constantly exposed to high levels of friction and heat. The fumes generated during the machining process pose a significant risk of fire or explosion within the machine’s enclosure. Errors in programming or mechanical malfunctions can swiftly escalate a routine machining operation into a hazardous situation. Even a minor spark can rapidly ignite the coolant oil and vapour, leading to a major fire within seconds. Consequently, this can result in lost productivity, customers, profits, market share, property damage, recovery costs, and, worst-case scenarios, loss of life.
Advantages/ disadvantages of oil-based fluids
Straight oil-based metalworking fluids, coolants, and lubricants offer various benefits over water-soluble alternatives in industrial CNC and EDM machines. Using oil-based metalworking fluids in industrial CNC and EDM machines will increase tool life, reduce friction and heat, improve surface finish and help flush dross from the work area. The greatest advantage of straight oils is their excellent lubricity or “cushioning” effect between the cutting tool and workpiece.
This is particularly desirable for applications that require high-quality surface finishing. The greatest disadvantage of straight oils is their poor heat-dissipating properties, which leads to an increased fire risk. This is why they are usually limited to low-temperature and low-speed operations.
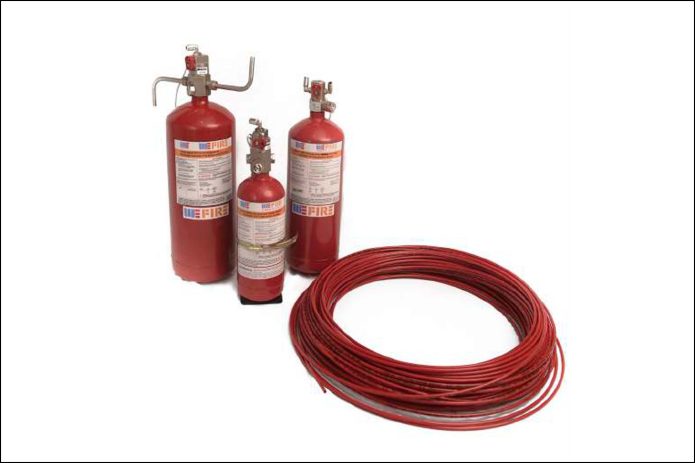
Titanium Fires
Titanium is the only metal with remarkable strength, low density, and exceptional corrosion resistance. Industries like aerospace and medical implants seek precisely machined titanium components with tight tolerances. Despite titanium’s low flash point, some shop owners shy away from machining it due to fears of fire hazards in their machinery.
While titanium presents a potential fire risk, the common belief about its primary role in machine fires must be corrected. Most fires originate in coolant oils with a significantly lower flash point than titanium. As these fires escalate, the enclosure’s temperature rises enough to ignite titanium, but the initial ignition source often lies within the coolant oils.
Hence, the solution lies in the early detection of oil fires at their initial stages to prevent the temperature from reaching levels where titanium could ignite.
Containing machine fires threatInstalling an automated fire detection and suppression system is a dependable and economical method to safeguard your CNC machines against fire risks and the subsequent losses due to machine disruptions. However, not all fire protection systems are equal. The trick is to bring the fire detection and suppression apparatus into the micro-environment of the machine itself to detect and extinguish a fire at its source quickly.
One such effective and proven solution by WEFIRE™, relies upon heat-sensitive pressurized tubing as detection. The tubing can react to a fire in a few seconds and deliver total suppression in less than 15 seconds using a clean agent such as Novec 1230, FK5112, HFC or CO2. Alternatively, a WEFIRE system can also be activated manually or using an Industrial grade UV/IR flame detector. The pressure switch mounted on the cylinder of the WEFIRE system can additionally be used to trigger an alarm or for auto damper shut-off, auto door closure, etc.
Using the WEFIRE system swiftly identifies and extinguishes machine oil fires. Moreover, the clean agent employed doesn’t necessitate cleanup and won’t taint the coolant oil. Once the fire’s cause is resolved, most CNC machines can promptly resume operation.
Case study
A Pune-based crankshaft manufacturer had the WEFIRE™ automatic fire suppression system installed on their CNC machines. Originally using a water-based coolant, they switched to an oil-based coolant for their specific requirements. To accommodate the machine’s large grinding area of approximately 28m3, they connected three 20 lb clean agent cylinders in parallel, forming a 60 lb system. Heat detection tubes were placed on the machine’s roof and walls, complemented by six discharge nozzles strategically positioned in critical areas.
One evening, the ignition of oil fumes inside the machining enclosure occurred due to sparks from the spindle, resulting in a blast caused by the accumulation of flammable oil and fumes. The sudden flash fire escalated rapidly. Within moments, the heat detection tube mounted on the machine’s interior roof sensed the fire and triggered the WEFIRE system. Instantly, the clean agent extinguishes gas discharged from all six nozzles, flooding the entire compartment and extinguishing the fire within seconds.
Result
After this incident, the customer recognized the importance of installing a WEFIRE system. It swiftly extinguished the fire within seconds and limited the damage caused by the fire, preserving the machine, shop floor, minimizing downtime, and most importantly, protecting human lives.
In a short span, the WEFIRE™ system was reactivated, and the machine resumed its operations promptly, effectively continuing its primary function of “generating revenue.”
For further information, visit web: www.wepune.co.in
Email us on info@wepune.co.in
Cookie Consent
We use cookies to personalize your experience. By continuing to visit this website you agree to our Terms & Conditions, Privacy Policy and Cookie Policy.