Our defence supply chain will thrive only with homegrown, advanced materials
By Staff Report July 10, 2025 6:19 pm IST
India’s defence sector can change its face by focusing on domestic production of advanced materials and building a self-reliant supply chain that ensures consistent, cost-effective access to critical components essential for national security.
Over the last decade, there has been a greater thrust on indigenous manufacturing, including hi-tech futuristic defence systems. Several policy initiatives have encouraged active participation from domestic private players. There has been a buzz around R&D and innovation in solutions that employ high-performance engineered ceramics, composites, and new-age materials such as graphene. This has facilitated a renewed approach towards realising the core objective of defence, saving lives by enabling the most advanced protection for man and machine across terrain.
Despite these measures, India reportedly spends approximately Rs. 14,000 crores each year to import critical ‘military’ materials, as per KPMG’s report on ‘Military Materials – Challenges & Opportunities’. We are also completely import-dependent for certain defence-strategic materials that are unavailable. This assumption takes on greater importance in an era of intense geopolitical uncertainties and tightening protectionist tactics, such as higher import tariffs. It could have a detrimental impact on supply chains, resulting in prolonged disruptions. Ensuring self-sufficiency in material procurement is crucial to bolstering the domestic ecosystem.
The first step is to secure strategic domestic supply sources which are globally benchmarked and certified, independent of global marketplace challenges, at the most advantageous prices. Reducing dependence on imports of strategic defence materials can help bypass high raw material import costs and mitigate international supply chain disruptions.
This presents a good opportunity for Indian domestic players to enhance their supply chain and production capabilities to meet the growing demand. With the use of indigenous materials, high-quality defence requirements such as body armour and vehicle armour can be made widely accessible through reduced costs while maintaining world-class quality.
Building a strong and resilient supply chain
As warfare tactics evolve, key requisites for protective defence equipment, such as body and vehicle armour, are not limited to providing maximum protection. They also need to provide ease of mobility, high performance, and efficiency at an optimum cost. To do all this, they require cutting-edge materials with assured supply.
Take the case of armour. High-strength yet bulky metals, such as steel, have given way to tough yet lightweight advanced ceramics, including Reaction Bonded Silicon Carbide, Boron Carbide, high-purity alumina, and Zirconia-toughened Alumina. These materials enhance ballistic performance without compromising manoeuvrability or mobility due to their extremely lightweight properties. Boron Carbide and Silicon Carbide, with their exceptionally high hardness, can dissipate compressive stress considerably, offering protection from high-impact projectiles. They have also been rigorously tested and have consistently emerged at the top. A recent instance is CUMI’s ceramic composite armour panels, which have been successfully tested and qualified in line with STANAG 4569 (2&3) protection levels by the global accreditation agency IABG.
However, factors such as affordability and unavailability of materials are proving to be a challenge.
Leading players in materials science, such as CUMI, can help bridge such gaps. Being backwards-integrated – from sourcing raw materials (grains and powders) to manufacturing ceramic components that go into body and vehicle armour – can help local manufacturers fulfil growing demand and reduce import dependence. Moreover, continuous investment in R&D has also ensured the development of unique innovations with a high performance-to-price ratio. A good example is CUMI’s patented elastomeric ceramic armour panels. These lightweight add-on panels are custom-designed to fit the vehicle’s profile, offering additional armoured protection economically and accurately. In 2024, CUMI was awarded a Transfer of Technology from DRDO-DMRL to manufacture these composite armour panels for the indigenously designed WhAP 8×8 and other armoured vehicles.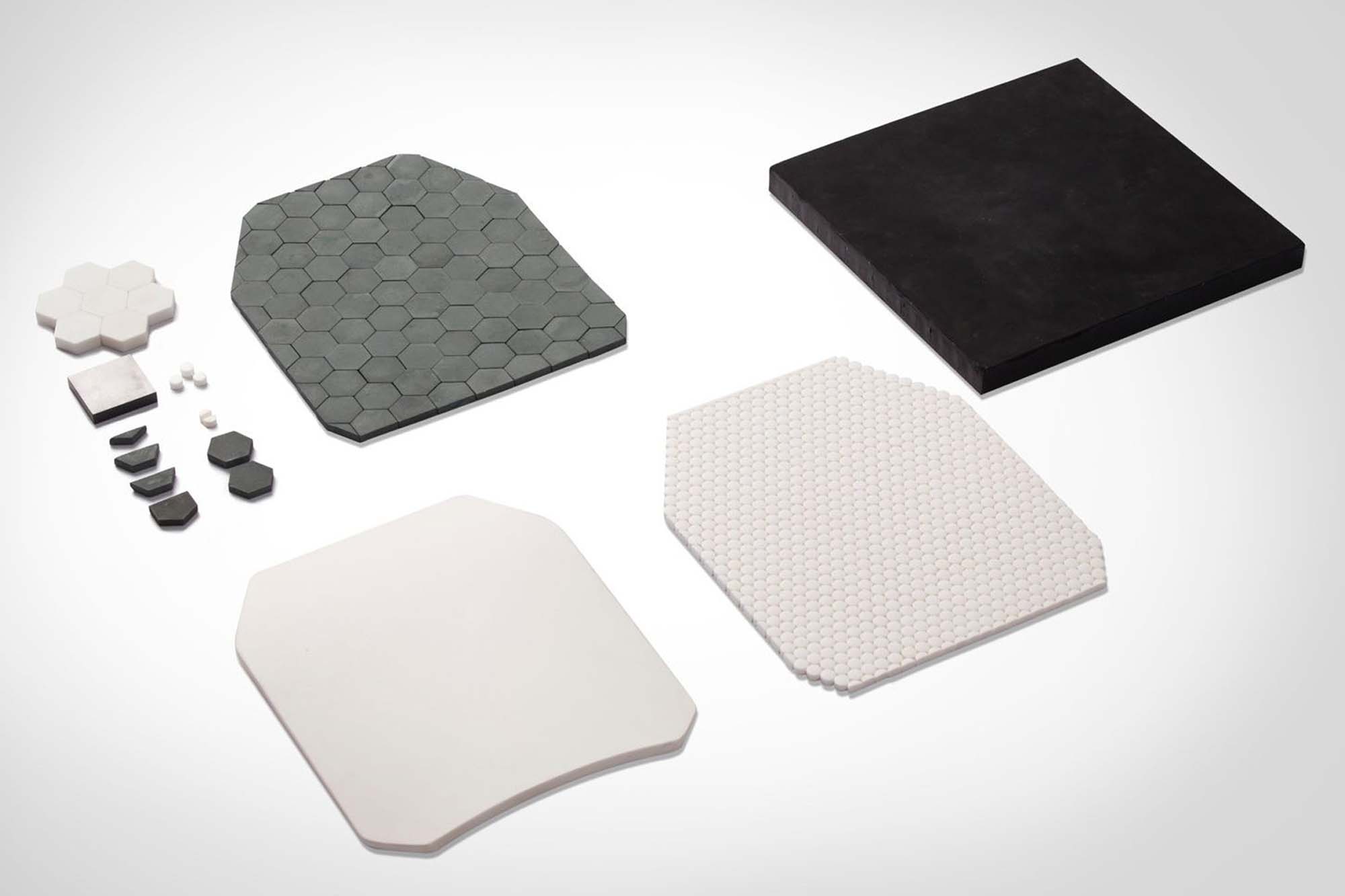
Global certifications and standards
Adherence to global benchmarks, standards and certifications is a mark of trust and the highest quality in the defence and aerospace marketplace. Since it involves the protection of man and machine, defence-critical materials are subject to stringent guidelines. For instance, the NIJ global standard for bulletproof vests, STANAG for vehicle armour and international quality certifications such as the EN9100 (also known as AS9100D) define rigorous standards for quality. Increasingly, the government’s mandate and the focus of domestic manufacturers on globally certified materials are ensuring the large-scale modernisation of India’s defence, putting the Indian industry on par with the best globally. This also means that OEMs can now access a comprehensive library of globally certified materials manufactured indigenously.
Addressing the cost element
Several factors work in tandem to determine material cost. Important among these are material availability and grade. Applications in defence and aerospace require premium-grade, high-purity, and superior-strength materials, where the price can prove prohibitive and unsustainable for long-term import. Higher grades mean a greater number of processes are involved in creating uniformly ultra-fine powders, rendering the material more expensive to produce.
Concurrent demand from other sectors also serves to drive up the cost of base materials. At times, a lengthy production process with restricted batch quantities can impact the price. Factoring in all of these, indigenous sourcing and production of critical materials presents a far better value proposition.
India continues to spend heavily on defence imports, although this has seen a steady downward curve over time. Volatile exchange rates, fractured global alliances, and supply disruptions drive up material costs. This means that importing at global prices with the final product manufactured in India will defeat the larger ambition of indigenisation.
Relying on fully integrated domestic players is crucial for strengthening India’s defence sector. By investing in advanced research and production, these players can meet the demand for new materials at competitive prices, helping to diversify funding towards indigenously produced solutions. This approach will provide the private security market with cost-effective options and boost exports through strategic pricing. Ultimately, these efforts will enhance India’s domestic defence supply chain and strengthen its strategic capabilities for both the defence sector and private players.
Cookie Consent
We use cookies to personalize your experience. By continuing to visit this website you agree to our Terms & Conditions, Privacy Policy and Cookie Policy.