Machines will think along with us in the future
By Staff Report July 24, 2025 11:30 am IST
Industrial manufacturing is undergoing a major transformation as artificial intelligence (AI) is integrated into machine tools, enhancing production processes and machine maintenance. AI is becoming essential for efficient, sustainable, and competitive production in the face of skill shortages and international competition. Discover how AI is revolutionising industrial production at EMO Hannover 2025, the leading trade fair for production technology, from September 22 to 26.
AI in machine tools means much more than just automation. It enables machines to learn from data, make decisions and optimise processes. Sensor technology, data analysis, machine learning and intelligent assistance systems are used for this purpose – both at the control level and in interaction with people.
Increasing the individual potential of AI
There are many possible applications for manufacturing companies: “Typical examples would be the prediction of process properties in real-time operation for inline quality control and the monitoring of processes and their properties,” says Prof. Philipp Klimant, Head of Business Unit Process Digitization and Manufacturing Automation at the Fraunhofer Institute for Machine Tools and Forming Technology (IWU) in Chemnitz. “The advantage over traditional approaches is the ability to include a particularly large number of parameters in the monitoring process,” highlights Prof. Klimant. However, there are also numerous other fields of application, such as AI assistance models for training and artificial intelligence to support maintenance. The Fraunhofer IWU, which specialises in the production-related adaptations of traditional and modern machine learning methods, is headed by the trio of Martin Dix, Welf-Guntram Drossel and Steffen Ihlenfeldt. All three are members of the WGP (Wissenschaftliche Gesellschaft für Produktionstechnik/German Academic Association for Production Technology), an association of leading German professors in the field of production science. As of January, the WGP has consolidated the ProKI initiative, which was originally funded by the BMBF, under its umbrella and has since been offering highly practical expertise and demonstrators, especially to small and medium-sized companies that want to find out about the potential of AI for their individual situation and/or are looking for support.
Great leverage for efficiency gains
The IWU researcher’s tip is to ask the following question at the very beginning: How large are the efficiency gains that are actually possible through AI in my production process? “The question of what efficiency gains are possible cannot be answered universally without further analysis,” says Prof. Klimant. The potential is heavily dependent on the actual process and the associated optimisation possibilities. “In the field of plastics processing, injection moulding, for example, reject rates of 20 to 30 percent can occur in rare cases.” This represents a major lever for efficiency gains with AI. It can also be useful for processes that are already running with a high level of stability, for example, in the area of predictive maintenance, and to achieve longer service lives of tools.
According to Prof. Klimant, artificial intelligence can also make an important contribution to alleviating the shortage of skilled workers. “We store knowledge implicitly in AI. This knowledge can be used to train new employees, especially when older colleagues retire and important knowledge leaves the company,” explains the scientist, who has also been Professor of Virtual Technologies at Mittweida University of Applied Sciences in Saxony since 2023. “This repository of AI knowledge also offers new opportunities for automation, not least for automated quality control,” says Prof. Klimant.
The researcher defines artificial intelligence as follows: “When we talk about AI, we usually mean machine learning as a subgroup of AI. This can learn independently from training data. It is an empirical process that learns correlations without us knowing the analytical correlations. Simply put, we learn from experience.” AI is used to optimise the process parameters in production and feed them back into the process controller via an automated control system. “Artificial intelligence is like a black box, input values go in and forecasts come out,” says Prof. Klimant. “One example of this would be a forming process where we measure an acoustic signal and then the AI tells us whether or not the process was successful.” Ultimately, it is a digital system that can be connected to control systems via existing interfaces. This allows AI to influence control algorithms at various points.
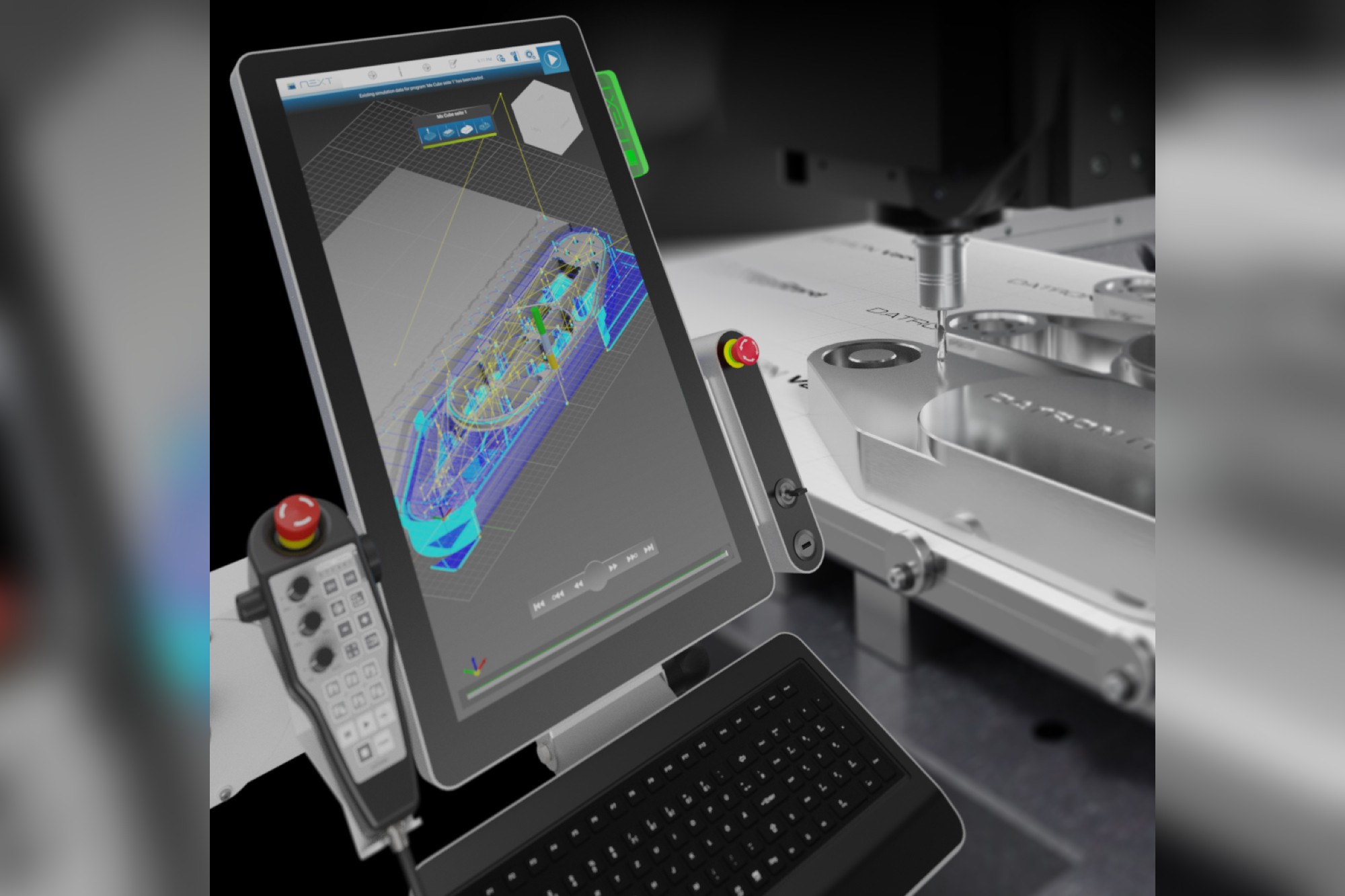
High computing power for image processing
In order for artificial intelligence to be used successfully in production, hardware with very high computing power is sometimes required. “First of all, a distinction must be made between the training phase and the utilisation phase (inference). The training phase is always more computationally intensive, but is carried out offline. In the utilisation phase, edge devices are often sufficient for classic methods such as the support vector machine,” says Prof. Klimant. The situation is different when it comes to the topic of image processing. These AI models require more computing power, both in the training phase and in the utilisation phase. “The application cycle also plays a decisive role here,” explains the researcher. “If I need a result every five seconds, for example, I will need more computing power compared to a cycle time of 30 seconds.” The evaluation of language models represents an exception here. These require powerful hardware, from high-performance consumer graphics cards through to special AI cards.
Self-learning machine tools enabling autonomous production
Self-learning machine tools are made possible by AI. Milling machine manufacturer and EMO exhibitor Datron AG from Ober-Ramstadt near Darmstadt makes use of this innovation, in which the machine draws on learned knowledge and adapts the production process. The aim is to develop Datron milling machines into adaptive production cells that automatically adjust to component requirements and environmental conditions. “This not only reduces set-up and machining times, but also increases process stability – a decisive step towards autonomous production,” says Jonas Gillmann, Chief Technology Officer (CTO) of the publicly listed mechanical engineering company.
AI is thus shifting the focus away from rigid programming towards assisted, self-learning and adaptive production. “Machines are becoming partners in the manufacturing process, which adapt to humans – not the other way around. In mechanical engineering, this is no longer a vision, but is increasingly becoming a reality,” says Mr. Gillmann. As he explains, AI in production offers high levels of efficiency gains: “In CNC production with Datron machines, it can reduce set-up times by up to 60 percent, significantly reduce the amount of rejects and extend the service life of tools – while at the same time increasing process reliability.”
Intuitive guidance through the milling process
One particularly exciting advance is the link with the “Datron next” control software, says Mr. Gillmann. This guides even inexperienced operators intuitively through the milling process and automatically recognises workpieces. “This means that even employees who are not specialised in the technology can perform milling productively – a clear advantage in view of the shortage of skilled workers,” says the Datron Chief Technology Officer, who started his career as an industrial mechatronics technician at the milling machine manufacturer from Hesse. According to Mr. Gillmann, AI will in future also allow predictive maintenance to be carried out in order to prevent failures before they occur. “This will make the milling process more efficient, more robust and much more flexible in terms of the personnel required.”
Artificial intelligence in machine tools can also help to meet the increasing demand for customer-specific products with small batch sizes. “AI makes the production of small batch sizes economical: With the Datron next control software, workpieces are recognised automatically – without complex programming,” says Mr. Gillmann. “This eliminates the need for long set-up times, and individual parts can also be manufactured quickly, efficiently and to a high level of quality – which is ideal for customised products.”
Less programming, more process responsibility
Self-learning machine tools are also changing the job description of the user: “Less programming, more process responsibility,” is how the Datron CTO sums up the change. Employees are becoming process designers who ensure quality and optimise processes. “This lowers the barrier to entry and human expertise is supplemented – not replaced – by smart assistance.”
AI as the key to competitiveness
The use of artificial intelligence in factories is helping to meet three major competitive challenges. Firstly, AI is helping the industry to alleviate the shortage of skilled workers through automated assistance, intuitive user interfaces and self-learning systems. In cases where specialised machine operators used to be necessary, staff with all-round technical skills will suffice in the future.
Secondly, AI increases sustainability by minimising rejects, optimising energy consumption and enabling condition-based maintenance. This conserves resources, reduces emissions and lowers material consumption – a key selling point in view of climate-conscious industrial policy.
And thirdly, the use of AI is a response to the high level of international competitive pressure. Whoever produces faster, more efficiently and more flexibly will end up as the winner. Artificial intelligence makes it possible to react to market changes in real time, allows the production of small batches without the need for set-up and increases machine utilisation rates – an important key to remaining competitive in Asia, Europe and the USA. Machines that were once purely mechanical systems are now becoming self-learning units.
AI in machine tools is no longer a vision, but part of everyday industrial reality – with immediate advantages for productivity, quality and sustainability. In the face of global upheaval and pressure to achieve greater efficiency, the self-learning machine tool is becoming the cornerstone of industrial sustainability – and represents an opportunity for Germany as an industrial location.
Cookie Consent
We use cookies to personalize your experience. By continuing to visit this website you agree to our Terms & Conditions, Privacy Policy and Cookie Policy.