The right machine at the perfect time
By Staff Report October 8, 2024 8:08 pm IST
How do you select the right machines for manufacturing large-size stamping dies? Avinash Khare, Consultant and Corporate Trainer, walks us through the multitude of machines and their pros and cons, depending on the situation.
So how large is it? Large stamping dies used for automotive panels could measure up to 4.5m x 2.5m x 1.5m and weigh up to 20 Tons. The machines required to manufacture these dies must be made of an even larger mass of steel and could have a working volume of 6m x 3m x 2.5m.
Unlike SPMs and mass production scenarios where only point-to-point accuracy and repeatability are required, and statistical methods can be applied, most die-making machines require calibrations for absolute volumetric accuracy.
- Even if the largest die may come only once in a while, any machines selected should be able to accommodate the largest die.
- Machines require many diverse features to cover various odd situations, but capability utilisation often remains poor.
- Most of the time, big machines are used for smaller dies, leading to uneven wear of slides and ball screws after some years of use.
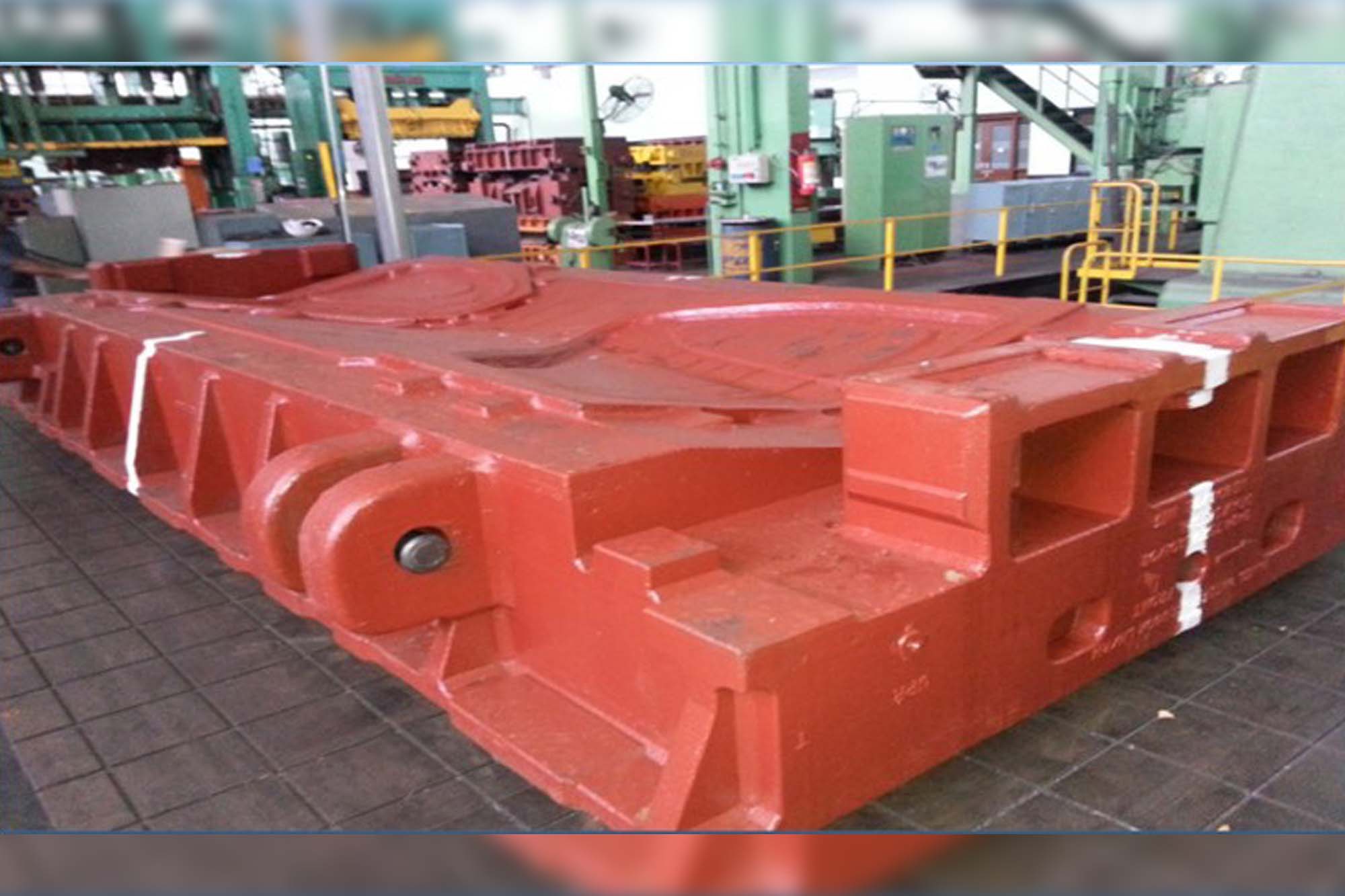
Different Machining Requirements
Different machining is required to manufacture dies, and each machining process poses vastly different demands on the machine tool and operating personnel.
Base Machining of Castings:
A planer or 2.5-axe Plano Milling Machine can take up to 10mm of cut depth with a 300mm diameter End Mill Cutter and spindle, with huge torque and lower RPMs.
Accuracy and finish are not required, but the flatness of the milled surface must be good.
The challenge is to invert the casting support to the free-form surface and level the base before taking the cut. An overcut or the wrong plane of cut can scrap the casting.
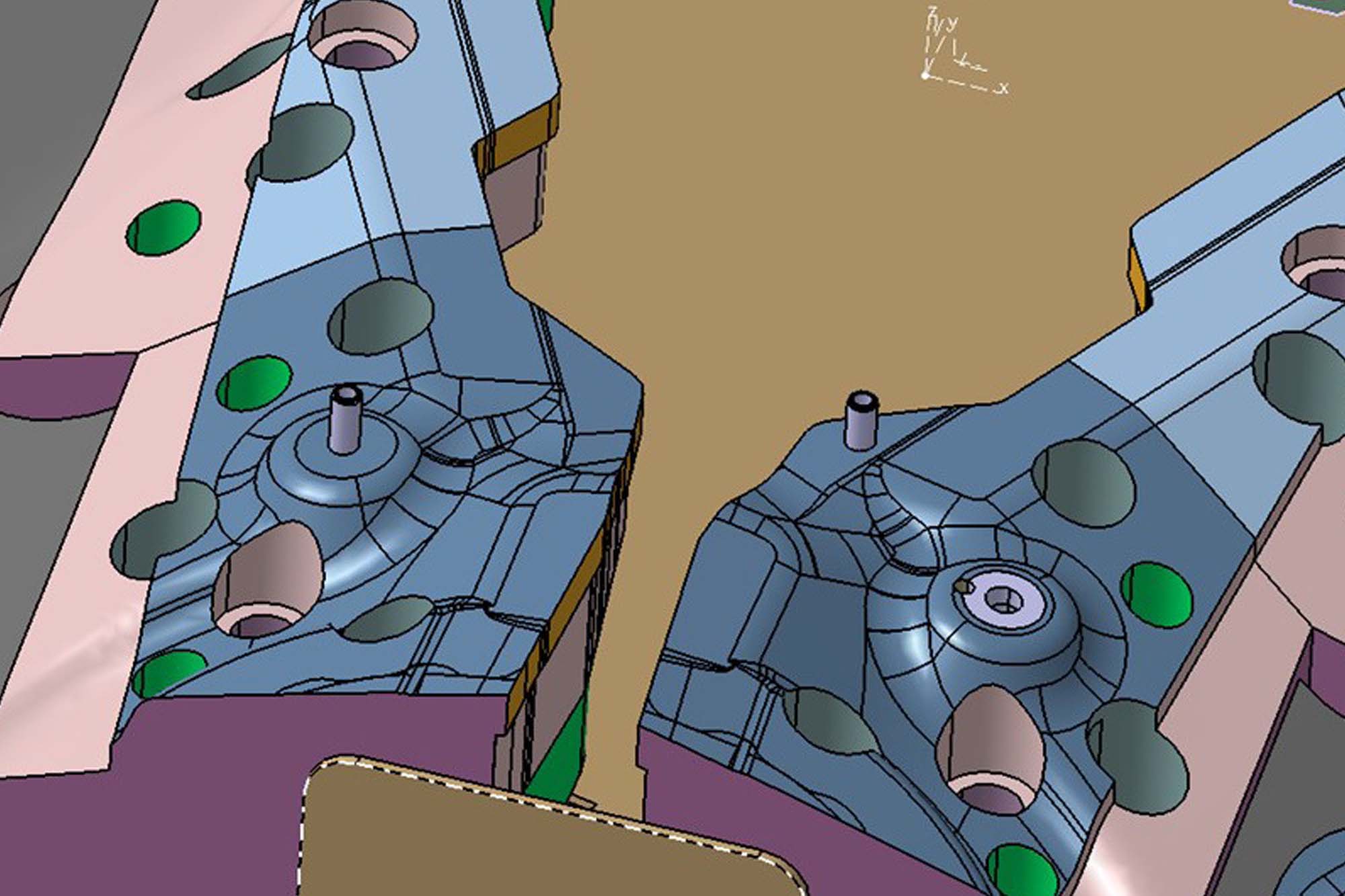
Milling and Boring of Geometrical Features:
Flat faces must be milled for wiper guides, mounting inserts, springs, spacer blocks, pad retainers, and CAM mounting faces. Boring is required for mounting pillars and bore guides.
Boring quill and feed/revolution of the spindle.
These operations deserve a family of spindle attachments for five-face machining and deeper and narrower access.
Drilling and Tapping:
Drilling and Tapping are for mounting provision dowels and venting holes.
Often, less sturdy manual radial drilling machines are used.
At times, heavy castings must be handled in precarious and unsafe ways and set up in precarious vertical positions.
The use of CNC machines for drilling and tapping is generally deemed underutilised.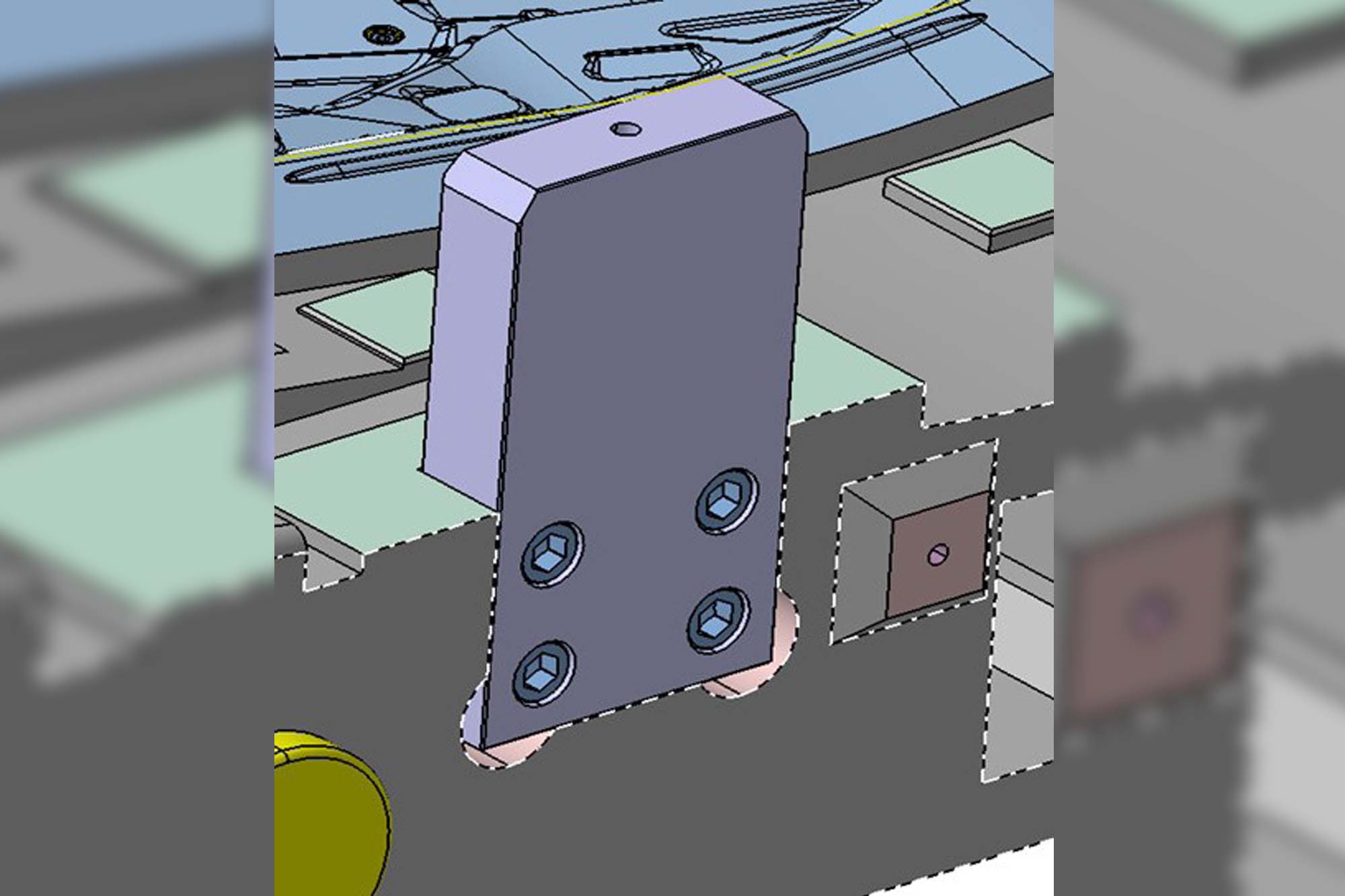
Free Form Surface Roughing:
These are sturdier 3-axis CNC machines. Roughing could be done with a high-productivity toric (scooping) cutter or by scanning with a larger (25- 50 mm diameter) ball nose cutter.
The spindle could have RPMs from 5000 to 10000.
Since stock removal could be uneven and casting could have sand inclusion in the upper layers, adaptive control is recommended to protect the cutter.
During roughing, cutters sometimes produce bands of different hardness on the die, and those patterns are seen in the stamping produced by crash forming machine structure breathe by something like 0.5mm over 24 hours due to daily variations in ambient temperatures.
A lot of hand polishing/grinding is inevitably required to match the upper and lower Dies for the base and back spotting of inserts and machines, and the machining crew is invariably blamed for this.
It is physics, not just linear thermal expansion/contraction. Machine/job distortion depends on multiple variables, such as temperature, air blow, local hot spots, temperature gradient, and rate of change of temperature. These effects are not repeatable and predictable.
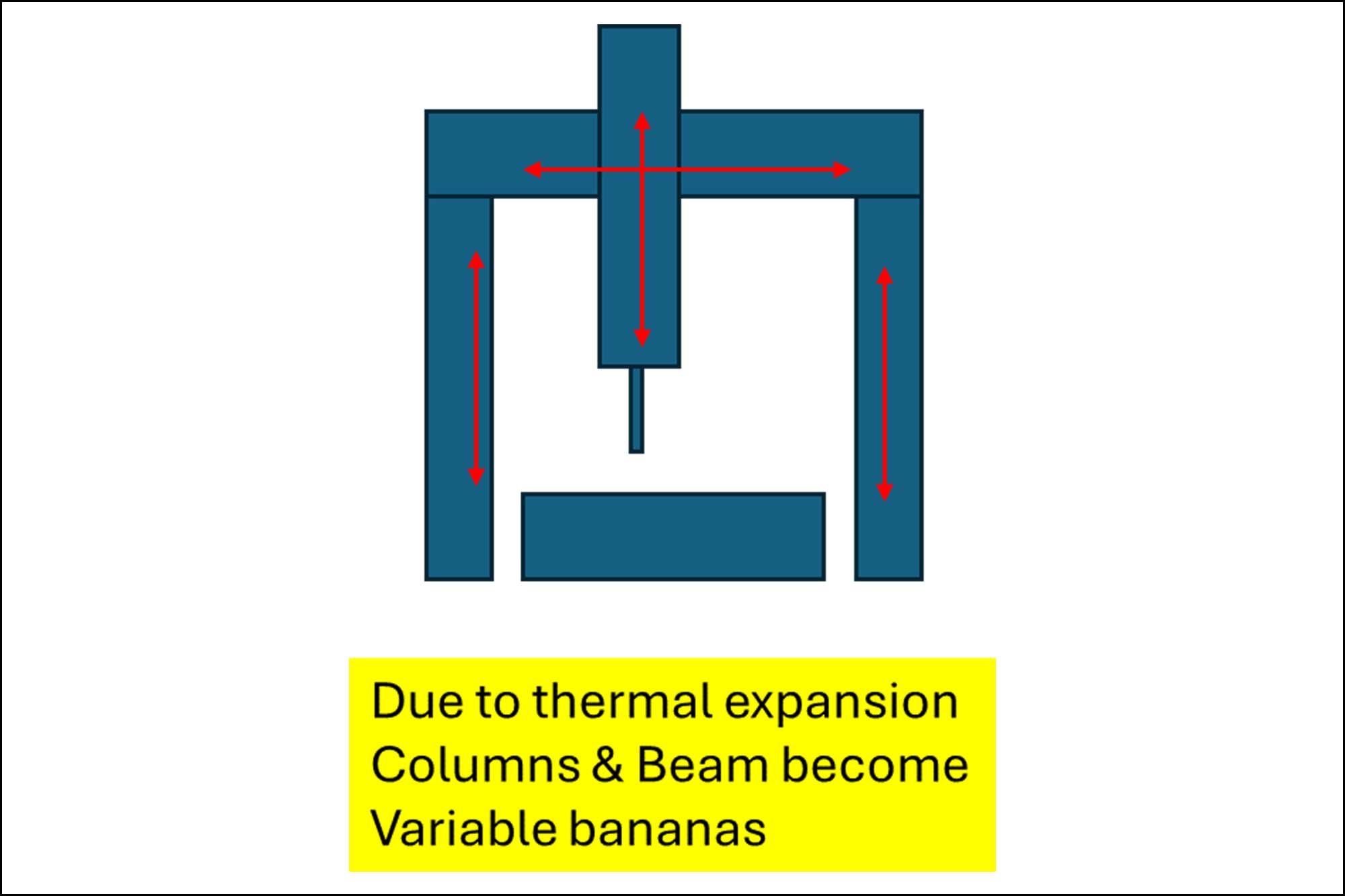
What kind of machine is better – Horizontal machine or Vertical machine?
Chips and coolants drop directly into conveyors at horizontal machines while they get scattered and filled into cavities when Vertical machines are used.
Usually, horizontal boring machines have a quiz and feed/revolution feature. They could even sport a Universal Head. Vertical machines must use a variety of attachments for five-face machining with deeper and narrower access to features.
Heavy jobs are loaded vertically on angle plates for Horizontal Machines, which is unsafe and time-consuming, while at Vertical Machines, the job could be simply kept at the table with a crane or forklift.
In horizontal machines, the spindle or quill droops down when they come out of guiding, while there is no such problem in Vertical Machines.
Moving Table Machine or Moving Column?
Moving Table Machines are sturdier on account of lesser cantilever magnification and cascading of all guiding clearances at the tooltip dynamics. Still, the Dynamic response of moving table machines depends on the job weight. Gantry and Moving Bridge / Column machines have fixed moving mass.
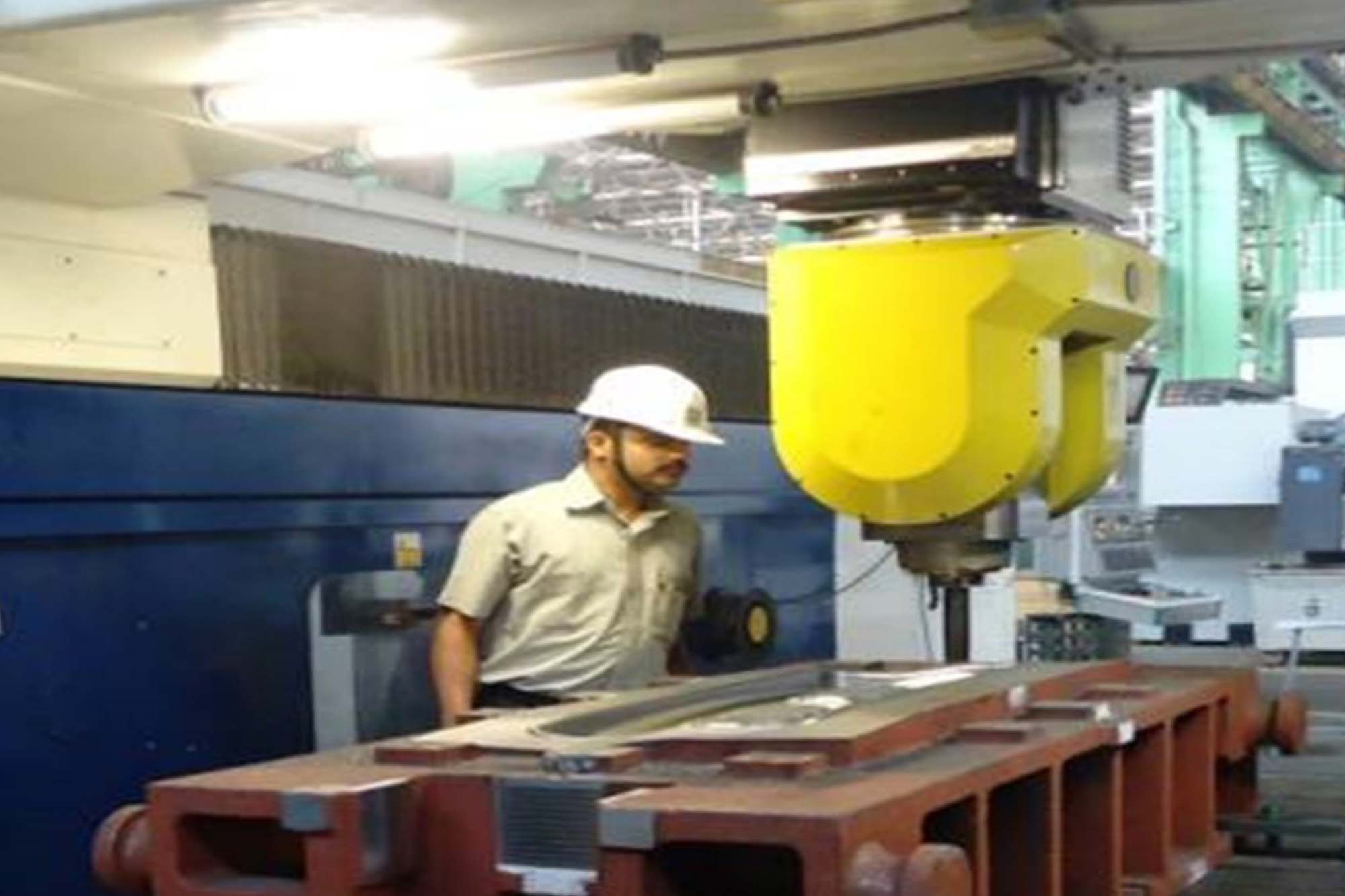
Conclusion: All kinds of machines have their boon and bane. The best approach is to have a variety of machines. Over time, skilled and dedicated personnel are bound to learn the best use of the machine for a given typical situation.
Ultimately, quality and performance do not automatically come from just a machine. They come from a combination of machines, a learning and adapting workforce, cutters, and CAD-CAM, and they have a lot of determined efforts in a hard, painstaking way.
Cookie Consent
We use cookies to personalize your experience. By continuing to visit this website you agree to our Terms & Conditions, Privacy Policy and Cookie Policy.