Integrating automation for MHE efficiency
By OEM Update Editorial February 28, 2024 3:18 pm IST
In an era where automation transforms industries, the material handling equipment (MHE) segment is no exception. Neeraj Waghela, Head of Product Development at ElectroMech Material Handling Systems (India) Pvt. Ltd., shares insights into how automation reshapes MHE processes, addresses workforce challenges, and drives efficiency and productivity in material handling.
How is automation being integrated into MHE cranes and hoists to improve efficiency and productivity in material handling processes?
Electromech seamlessly integrates automation into all its material handling equipment, employing a range of sensors and intelligent devices within its control systems. Integrating remote control functionality further enhances efficiency and productivity across our product lineup.
How do you evaluate the market for MHE with infrastructure growth and new product introduction?
The infrastructure sector has emerged as a key growth market for Electromech. It is essential in heavy material handling equipment like cranes and hoists on construction sites. Focusing on innovation, the company has introduced specialised products tailored for infrastructure applications such as the eRTG (Rubber Tyred Gantry Cranes) and STC (Steerable Transfer Car). Anticipating significant expansion in this sector over the next decade, Electromech plans to capitalise on the market demand with its versatile and manoeuvrable RTG. It is designed for precast handling and construction sites, needing no extra power supply or track for movement.
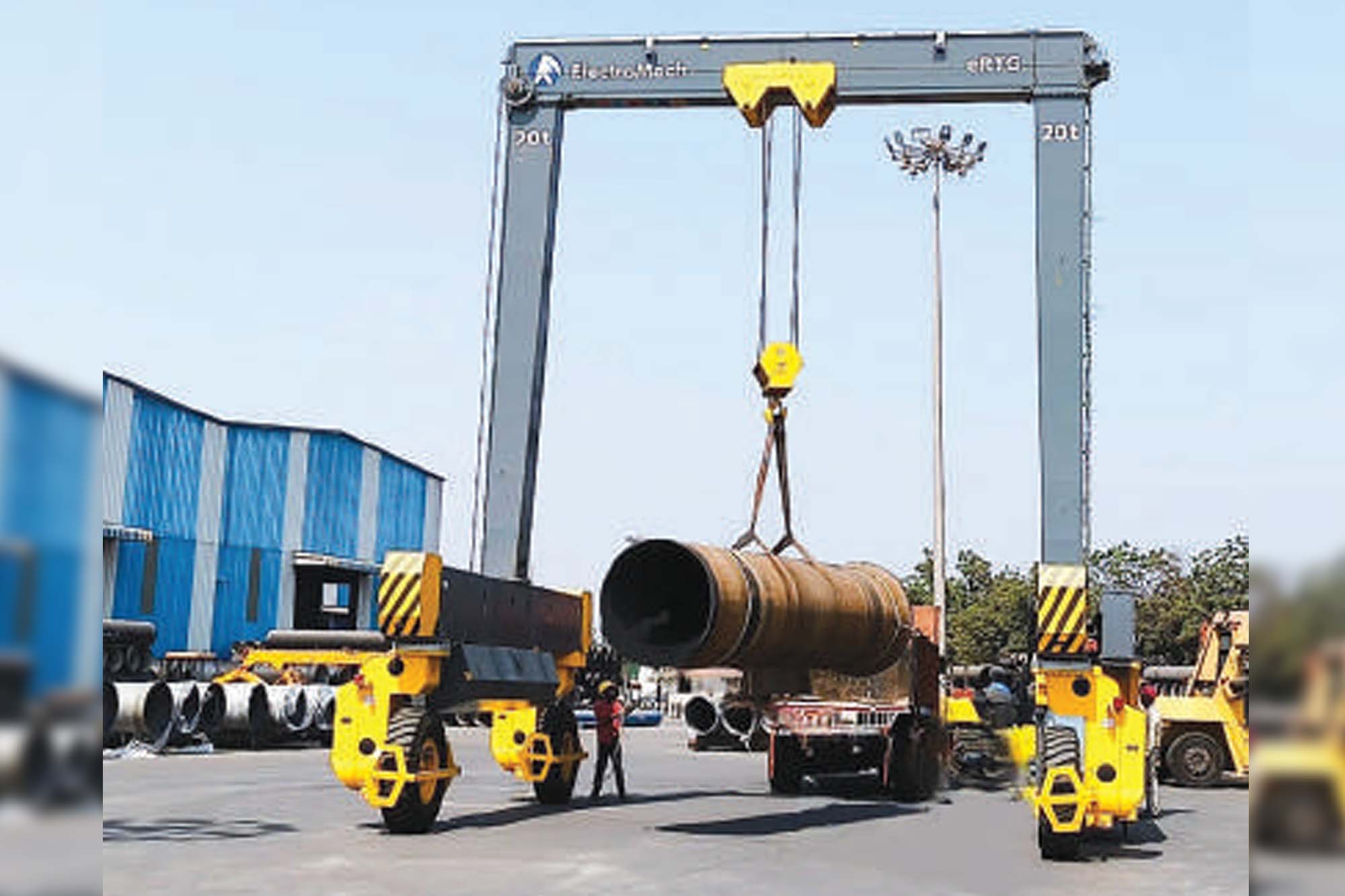
How does automation in MHE cranes and hoists address workforce challenges?
Automation is increasingly diminishing reliance on human intervention as safe and synchronised operations are paramount. The infrastructure and manufacturing sectors, particularly, are grappling with the challenge of maintaining a consistent workforce. Automation has now made the handling of heavy material equipment simple. It has streamlined the processes while reducing the need for extensive training. With remote control capabilities, operators can now efficiently manage equipment without experiencing significant fatigue, marking a significant advancement in operational effectiveness.What role do sensors and predictive maintenance play in optimising the performance of MHE to reduce downtime?
MHE automation relies on many sensors to capture distance, rotation, angle, temperature, current, and load data. These sensors enable seamless communication of all equipment movements to ensure precise control over their motions.
Electromech has developed “EMote” (remote monitoring system), an IoT device for equipment monitoring. Embedded within our machinery, EMote boasts a variety of sensors detecting vital metrics like current, load capacity, voltage, and energy consumption. This data is seamlessly transmitted to the cloud, granting users remote access to monitor equipment performance from anywhere. Such real-time insights offer invaluable advantages, facilitating the analysis of usage patterns and early detection of component irregularities. This proactive approach empowers predictive maintenance, ensuring optimal equipment uptime and performance.
What trends do you foresee for future MHE crane and hoist automation components?
While automation has been integrated into MHE operations for the past 5-10 years, ongoing developments are making significant advancements for the near future. These innovations hold great potential for enhancing overall industry efficiency. Electromech boasts a dedicated team committed to pioneering new solutions within the MHE sector, ensuring continuous progress in this field.
Cookie Consent
We use cookies to personalize your experience. By continuing to visit this website you agree to our Terms & Conditions, Privacy Policy and Cookie Policy.