Leverage advanced robotics for precision manufacturing
By OEM Update Editorial June 5, 2024 6:12 pm IST
Precision assembly is paramount in the competitive manufacturing field. Giulio Dal Lin, Carel Group Head of Lean and Process Innovation, highlights focus areas for leveraging advanced robotics in manufacturing processes and says that to scale up manufacturing efficiently, IIoT, 3D Printing and AI technologies should be integrated.
What technologies will you suggest to scale up manufacturing to optimise production efficiency?
Implementing technologies that enhance automation and efficiency is crucial to scaling up manufacturing effectively while keeping costs low.
Lean manufacturing techniques, such as Just-In-Time (JIT), can significantly reduce waste and storage costs by ensuring that components are ordered and received as needed. For instance, Toyota’s implementation of JIT has famously cut down their costs and improved their operational efficiency. In Carel, since 2006, we have been applying lean thinking with a company-wide approach to improve our processes continuously.
Another technology to consider is Advanced Manufacturing Execution Systems (MES), which integrate real-time monitoring to optimise production schedules and resources, reducing downtime and increasing output, and PLM, which enables an end-to-end management of product lifecycles. PLM is becoming a cornerstone of our engineering and production processes, letting Carel save time in the value chain creation process and improving the quality of products.
To scale up manufacturing efficiently while minimising costs, we need to integrate IIoT, 3D printing and AI technologies.
Utilise the Industrial Internet of Things (IIoT) by deploying sensors and connected devices to gather real-time data from equipment and production lines. This technology facilitates predictive maintenance, reducing downtime and prolonging equipment life. 3D Printing, also known as additive manufacturing, allows for rapid prototyping and the cost-effective production of parts with complex geometries. This technology reduces waste material and speeds up product development cycles. Finally, artificial intelligence (AI) should be implemented to enhance supply chain management and streamline production planning.
At Carel, we currently run several projects in those directions, striving to connect and automate different processes to enhance value to varied stakeholders.
What area should be focused on to leverage advanced robotics for precise assembly in manufacturing?
The focus should be on Cobot Integration Vision systems and Modular Robotics Systems to leverage advanced robotics in manufacturing.
Integrating cobots – collaborative robots designed to work alongside humans can increase safety and efficiency. In automotive manufacturing, cobots are used to assemble small, precise components, thereby increasing precision and reducing human error.
Equip robots with advanced vision systems to enhance quality control. These systems can detect invisible defects to the human eye, ensuring higher product quality. Lastly, implement modular robotics systems that can be quickly reconfigured for different tasks, increasing the flexibility and scalability of production capabilities.
To maximise robotics’ benefits, it is also essential to implement machine learning algorithms that allow robots to adapt to new assembly tasks through predictive analytics and automated adjustments, improving over time without manual programming.How do IoT and AI technologies assist in managing supply chains and ensuring quality control during manufacturing scale-up?
Scaling up manufacturing processes involves addressing challenges such as supply chain management, quality control, and workforce training. For instance, adopting the Internet of Things (IoT) or AI technology can help manage and monitor supply chains more effectively by providing real-time data on inventory levels, shipment statuses, and potential delays.
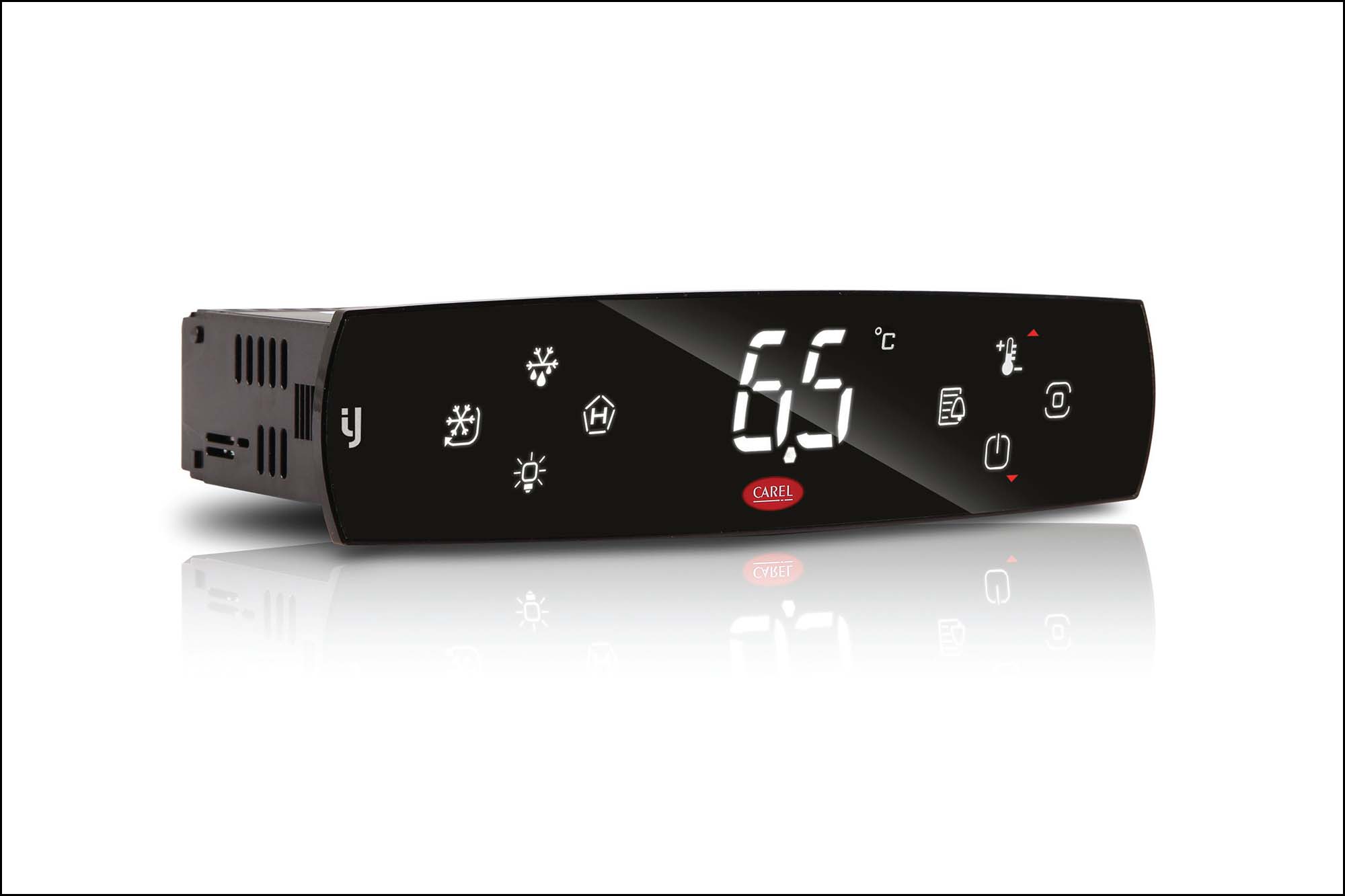
Investing in Total Quality Management (TQM) systems can help maintain product quality at scale by integrating quality control processes throughout the production cycle, not just at the end. The lean approach combined with Generative AI support could represent a front-edge application for further developing Carel performances.
Please talk about integrated elements to support upskilling and worker empowerment.
Integrating various elements that support worker upskilling and empowerment is crucial to developing a culture of continuous learning.
Adopt a lean leadership approach, where leaders act more as facilitators than bosses. This leadership style focuses on valuing each employee’s contribution and eliminating waste through continuous improvement. Leaders should promote an environment that encourages experimentation and learning from failures. It is essential for innovation and efficiency.
Implement a continuous coaching program where leaders and supervisors actively support employees in developing their skills and careers. Coaching helps personalise learning and adapt it to the specific needs and professional aspirations of workers, fostering personal and professional growth. Ongoing training and decentralised decision-making encourage an environment where decision-making is not centralised but distributed among teams.
It improves the speed and effectiveness of decisions. It also makes workers feel more involved and empowered, increasing their motivation and commitment. In Carel, we recently developed a so-called ‘Culture Code’ – a kind of internal manifesto for promoting such behaviours as “Experiment, Making the difference, Care, Thinking customer first, and Being open”.”These behaviours are fundamental for enhancing an internal culture that is striving to address the future in the best way.
Do you think scaling up a business without changing the operational approach can lead to unsustainable practices?
Scaling up without adapting the operational approach can indeed be unsustainable. As a business grows, the systems, processes, organisational structure, and strategies that work at a smaller scale might no longer be effective. Continuous improvement, evolution, and adaptability are crucial for sustainable growth.
Cookie Consent
We use cookies to personalize your experience. By continuing to visit this website you agree to our Terms & Conditions, Privacy Policy and Cookie Policy.