Advanced steels meet GFRP
By Staff Report July 10, 2025 6:52 pm IST
Glass and fibre-reinforced plastics are formed by embedding glass fibres into a polymer matrix. This creates parts that are strong, lightweight, thermally stable, and resistant to corrosion and electrical conductivity. This creates parts that last longer and weigh less, which makes them ideal for use. Partnering with technology providers like voestalpine Böhler Edelstahl can make the selection process even simpler.
The materials shaping the future of manufacturing are evolving. Among them, Glass and Fibre Reinforced Plastics (GFRP) can deliver lightweight, durable, and corrosion-resistant solutions across a range of demanding applications. Initially utilised in insulation, these materials are now integral to the automotive, aerospace, energy, and consumer electronics sectors.
Yet, the rise of reinforced plastics presents unique challenges, particularly when it comes to tooling. As industries seek better ways to mould and process these abrasive materials, traditional tool steels are reaching their performance limits. That is where advanced powder metallurgical steels are changing the game.
GFRP and the shift from metals to reinforced plastics
GFRP is a composite material formed by embedding glass fibres into a polymer matrix. This combination results in parts that are strong, lightweight, thermally stable, and resistant to corrosion and electrical conductivity. This creates parts that last longer and weigh less, making them ideal for a wide range of applications, from car components to wind turbine blades.
GFRP is rapidly replacing metal in several applications as industries strive to meet sustainability goals and reduce weight and emissions. The automotive sector is leading the way, replacing steel components with reinforced plastics to meet emission standards and improve fuel efficiency. Aerospace and renewable energy industries are catching up.
Plastic injection moulding meets reinforced plastics
Plastic injection moulding has become the go-to process for producing high-precision, high-volume parts. When combined with reinforced plastics like GFRP, the process offers unparalleled flexibility and efficiency.
Key trends reshaping this space include:
- Use of advanced materials such as bioplastics and fibre-reinforced composites to enhance product durability and lifespan.
- Adoption of Industry 4.0 technologies, including AI, IoT, and data analytics, to optimise moulding conditions and reduce cycle times.
- Sustainable practices include closed-loop recycling and reduced energy consumption.
- Simulation and predictive modelling that enable accurate performance predictions and reduce development time.
- Emerging moulding techniques like micro, LSR (liquid silicone rubber), and multi-material injection to support complex designs.
Challenges of conventional steels in GFRP applications
Despite GFRP’s advantages, its abrasive nature is notoriously harsh on mould materials. Conventional steels, such as 1.2344, 1.2379, and 1.2083—widely used in tooling—struggle to withstand the aggressive wear and stress introduced by reinforced plastics.
- 1.2344/H13, known for its suitability for hot work applications, fails due to abrasive wear caused by glass fibres, resulting in premature tool wear and costly maintenance cycles.
- 1.2379/D2, a high-carbon, high-chromium tool steel, exhibits brittleness and premature surface degradation in high-pressure, high-temperature GFRP moulding environments.
- 1.2083, valued for corrosion resistance and polishability, lacks the robustness to withstand extended exposure to high-glass content materials, particularly in mass production.
This performance gap necessitates a new class of materials that can endure the stresses of reinforced plastics while maintaining dimensional accuracy and surface finish over long production runs.
Powder Metallurgical (PM) steels, particularly those developed by voestalpine Böhler Edelstahl, are proving to be the ideal match for tooling in GFRP applications. Through advanced metallurgy and fine-tuned processing, PM steels offer:
- Superior hardness and toughness
- Improved wear resistance under abrasive conditions
- Homogeneous microstructure for better performance consistency
- Excellent machinability and polishability
- Customisability based on application-specific requirements
PM steels are manufactured using advanced powder metallurgy techniques that promote a fine, uniform carbide distribution and help minimise non-metallic inclusions. These characteristics make them particularly effective in tooling applications involving glass and fibre-filled polymers, where high abrasion and thermal stress are common.
Tailored steel solutions based on glass fibre content
Recognising that not all reinforced plastics are the same, Böhler offers a graded portfolio of PM steels optimised for different percentages of glass fibre content. Whether the application involves low filler content or high GF levels exceeding 50%, these solutions are designed to offer the following:
- Extended tool longevity in abrasive environments
- Lower maintenance frequency, minimising production disruptions
- Enhanced surface finish and dimensional consistency
- Greater overall cost efficiency over longer production runs
These material options consider factors such as filler length, additive materials (e.g., ceramics or metal oxides), and thermal cycle requirements, offering unmatched precision and performance along with glass fibre percentages.
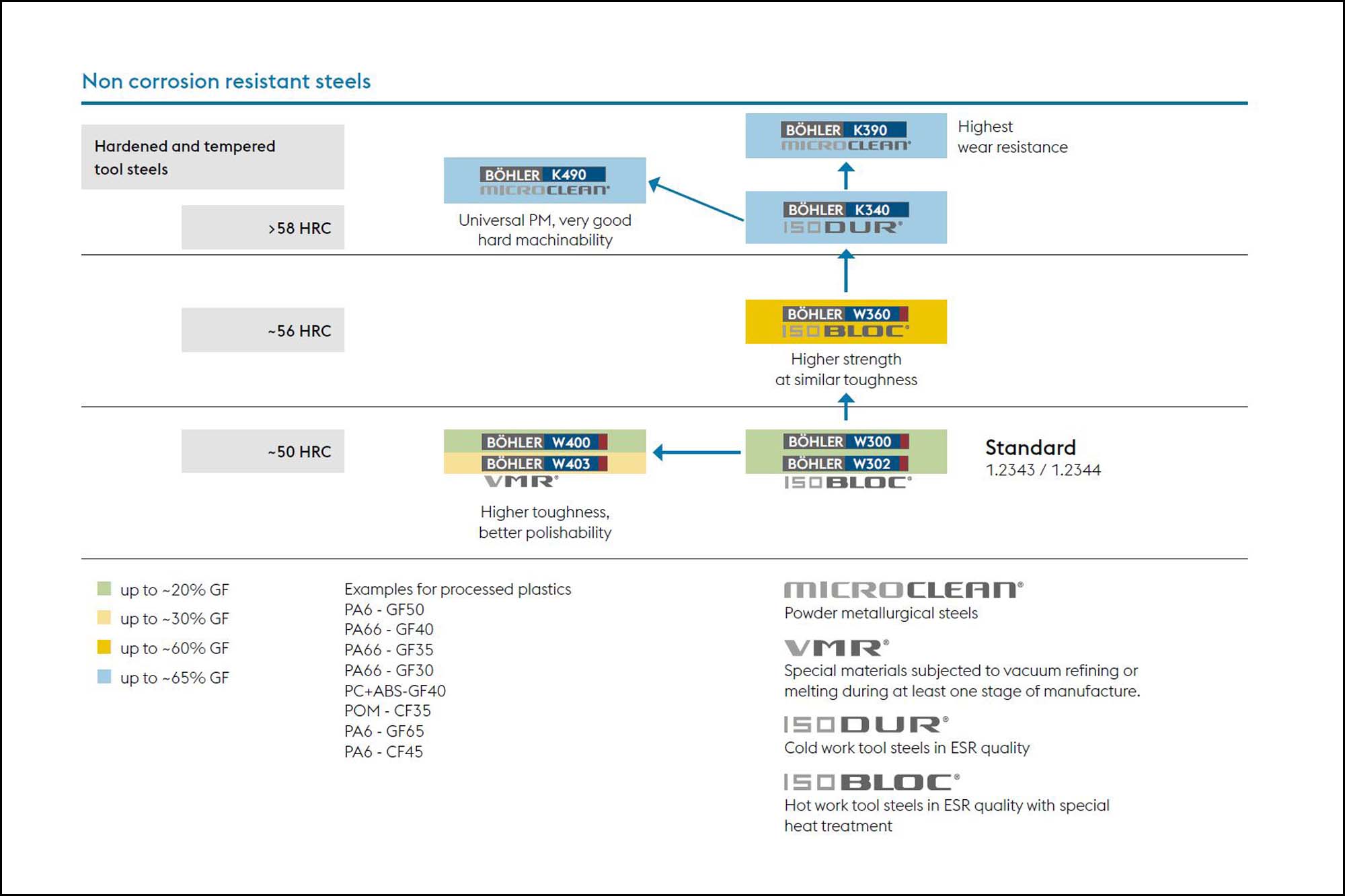
The future of reinforced plastics and tooling
As GFRP continues to gain traction across industries, manufacturers must adapt their tooling strategies to keep pace. According to Future Market Insights, the global demand for GFRP is projected to grow from USD 21.7 billion in 2025 to USD 47.3 billion in 2035, factoring in a CAGR of 8.1% in the forecast duration. This is facilitated by increased investment in renewable energy projects, as well as the development of improved infrastructure and manufacturing processes that continue to evolve.
In this shifting landscape, Böhler’s PM steels provide a crucial advantage, empowering toolmakers and moulders with the durability, flexibility, and performance needed to stay ahead.
Conclusion
The shift toward glass and fibre-reinforced plastics is more than a material change; it is a strategic move toward lightweight design, sustainability, and innovation. Yet, the tooling demands of GFRP require a level of steel performance that traditional grades cannot deliver. Böhler’s powder metallurgical steels can meet that challenge, offering moulders and manufacturers a resilient, future-proof solution tailored to the exact demands of reinforcement content and production complexity.
Cookie Consent
We use cookies to personalize your experience. By continuing to visit this website you agree to our Terms & Conditions, Privacy Policy and Cookie Policy.