Titanium machining for the aerospace industry
By OEM Update Editorial September 18, 2023 2:59 pm IST
Choosing the right tools helps overcome challenges associated with the complex machining of titanium, a preferred material in aircraft manufacturing.
The technologies deployed in the aerospace industry have undergone a radical transformation through the decades, resulting in aircrafts becoming compact, lighter, and more efficient. One of the major factors that has influenced the performance of airborne vehicles is the evolving dynamics of material science; yielding changing composition of metals used. Titanium, also known as a strategic material, is being used in increasing proportions today, accounting to almost 15% of the structure of these vehicles. Owing to its lighter weight and higher strength characteristics compared to other metals, impressive properties of corrosion and oxidation resistance, and easier availability overall, it is a preferred material for manufacturing critical parts. Yet, its poor machinability is recognised as an industry-wide challenge. Over the past few years, Kennametal has invested heavily in Research & Development to understand how to better machine titanium, and some of these findings, based on understanding its metallurgical properties are presented below.
Titanium undergoes various phases, from α to ß and depending on these phases, titanium alloys are classified into four main groups:
• Unalloyed/untreated titanium – excellent corrosion resistance, but lower strength properties
• Alpha structure (α alloys) – great creep resistance, and low to medium strength
• Beta structure (β alloys) – high strength and high density, but the most difficult to machine
• Alpha beta structure (α-β alloys) – medium to high strength, and include alpha and beta stabilizer elements
The commercially viable alloys are ß and (α-ß). Beta (ß) Alloys Beta (ß) alloys contain transition metals, such as V, Nb, Ta, and Mo, that stabilize the ß-phase. Examples of commercial ß alloys include Ti11.5Mo6Zr4.5Sn, Ti15V3Cr3Al3Sn, and Ti5553. Beta alloys are readily heat-treatable, generally weldable, and have high strength. Excellent formability can be expected in the solution treated condition. However, ß alloys are prone to ductile-brittle transition and thus are unsuitable for cryogenic applications. Beta alloys have a good combination or properties for sheet, heavy sections, fasteners, and spring applications
In comparison, α-ß alloys contain both α and ß stabilizers. The simplest and most popular alloy in this group is Ti6Al4V, which is primarily used in the aerospace industry. Alloys in this category are easily formable and exhibit high room-temperature strength and moderate high-temperature strength. The properties of these alloys can be altered through heat treatment.
Titanium is typically produced in the shape of plates and bars, as well as forgings and castings. The Buy-to-Fly (BTF) ratio is typically between 10 and 16, meaning a raw material of 10kg titanium ends up being a finished part with the weight of 1kg. The BTF ratio requires efficient removal of the excess material achieved through titanium roughing applications, which causes the cutting edge to be exposed to extremely high temperatures for a long time.
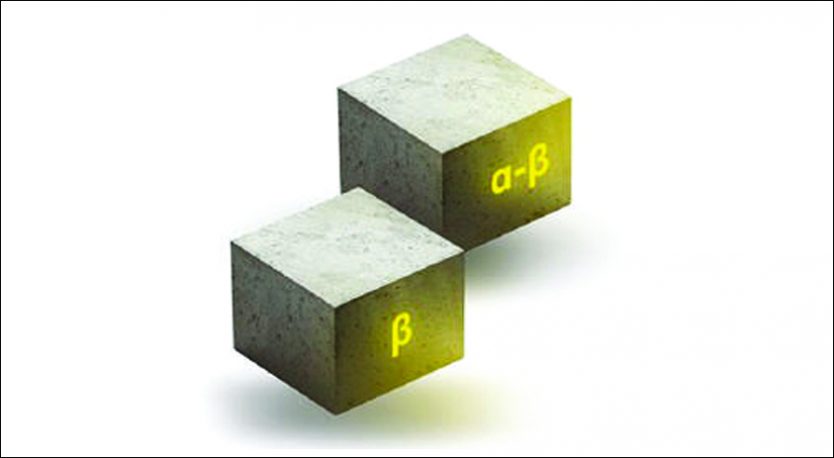
Some challenges associated with machining comprise high-chemical reactivity of titanium alloys, which causes the chip to weld to the tool, leading to cratering and premature tool failure. In addition, the chip-tool contact area is relatively small, resulting in large stress concentration due to these higher cutting forces and temperatures, resulting in premature failure of the cutting tool.
The machining of flight critical components (engine rotatives) at optimal production rates requires reliable, high precision tooling for semi-finishing and finishing turning operations. The entire process needs to be secured to avoid any damage to the part that requires advanced chip breaker technologies.
Requirements:
· Tool stiffness/stability
· Heat management
· Coolant flow· Grade toughness (chipping resistance)
· Heat-resistant coating
· Chemical wear resistance
· Micro geometry that promotes low cutting forces
· Stable machines and conditions that promote higher Metal Removal Rates (MRR)
Flat bottom drilling is ideal for pre-machining of high-temperature alloy airframe structural parts. Quickly removing large amounts of material remains a challenge for these types of components. Traditionally, the first step of the process is to enter the material by using ramping techniques, which is time-consuming and leads to low metal removal rates.
Speeding up the machining process requires combining the advantages of a flat bottom drill and a Z-axis plunge mill. The flat bottom design eliminates radial forces, while four effective cutting edges provide increased feed and speed rates, leading up to 200 percent higher metal removal rates than traditional ramping techniques and freeing up capacity for aerospace manufacturers.
Once the drill has shaped the basic structure of the component, it progresses for the roughing and finishing steps.
A recommended roughing solution for a large structural part is helical shoulder milling that addresses the high metal removal needs in aerospace machining. To achieve lowest possible cost per edge, tool makers have come with up to 8 cutting edges per insert in Helical Milling Cutters. Such designs are proven to reduce power consumption up to 50% and can deliver the highest MRR, especially in high-temperature alloys.
If the work holding is weak and tool overhang is high, another technique that can be used is High Feed Milling (HFM). With low entering angles, these cutters provide optimum cutting forces with maximum stability. Also, in materials like titanium which has extremely low thermal conductivity (thermal conductivity of Ti6Al4V is ~ 7.2 W/m K), it is prudent to work with higher feeds than speeds.
An array of new-generation PVD coatings with alloyed substrates are available, which provide resistance to thermal cracks, least co-efficient of friction and prevent chip welding in roughing applications. The cutter body should be constructed of higher-quality steel for improved stiffness and rigidity to withstand the high cutting forces. The variable helix design helps to break the harmonics that lead to chatter, further improving tool life, part quality, and throughput. Positive cutting action reduces vibration, minimizing the cutting zone temperature and prevents work hardening tendencies.
Finishing operations are mostly performed with solid endmills. Some unique design features include unequal flute spacing, variable helix configuration to minimize chatter and vibration, eccentric reliefs, twisted end face for increased stability and ramping along with the most optimized geometry, and flute design for titanium machining. In some advanced designs, endmills come with positive clamping technologies (safe lock) which prevent tool pull-out and ensure high process security. High-performance endmills will also have features like chip gashers for smooth chip evacuation and lower cutting forces.
Comprising high strength-to-weight ratio, corrosion resistance, fatigue resistance, and capability to work in high-temperature zones – titanium is usually the primary material for aerospace structures, frames, and engines. Titanium’s low modulus of elasticity, poor thermal conductivity, high chemical reactivity, and hardening properties, together, make it one of the toughest materials to machine. Therefore, an appropriate selection of cutting tool design and machining strategies is extremely important for machining titanium and its alloys along with proper machine, coolant and work holding capabilities, in order to maximize productivity and optimize costs.
(Content courtesy: Kennametal)
Cookie Consent
We use cookies to personalize your experience. By continuing to visit this website you agree to our Terms & Conditions, Privacy Policy and Cookie Policy.