Wipro 3D simplifies the move to industrial 3D printing
By Staff Report July 10, 2025 6:43 pm IST
Aerospace, defence, healthcare, oil and gas, and industrial tooling are witnessing the fastest adoption of metal AM in India. Wipro 3D supports businesses by demonstrating pilot projects, business case modelling, and real-world success stories, helping to simplify decision-making.
Wipro 3D, the additive manufacturing (AM) business of Wipro Infrastructure Engineering, helps clients integrate and scale additive manufacturing within their existing production ecosystems. With the holistic suite of services from consulting and design optimisation to prototyping, production, and post-processing, Wipro 3D enables a seamless transition to AM. The company also helps set up turnkey additive manufacturing centres equipped with metal and polymer 3D printers, allowing organisations to deploy in-house AM capabilities quickly. Wipro 3D focuses on aligning AM adoption with clients’ business objectives, helping them unlock value such as weight reduction, faster time-to-market, design freedom, and supply chain agility.
In India, the key industries showing the fastest adoption of metal AM include aerospace, defence, healthcare, oil and gas, and industrial tooling. Aerospace and defence lead adoption due to the demand for lightweight, high-performance parts and the flexibility AM offers for low-volume, high-value production. The healthcare sector is using AM for patient-specific implants and surgical instruments, while the oil and gas industry is adopting it for complex, high-performance components that withstand harsh environments—industrial tooling benefits from rapid design iterations and performance improvements enabled by AM.
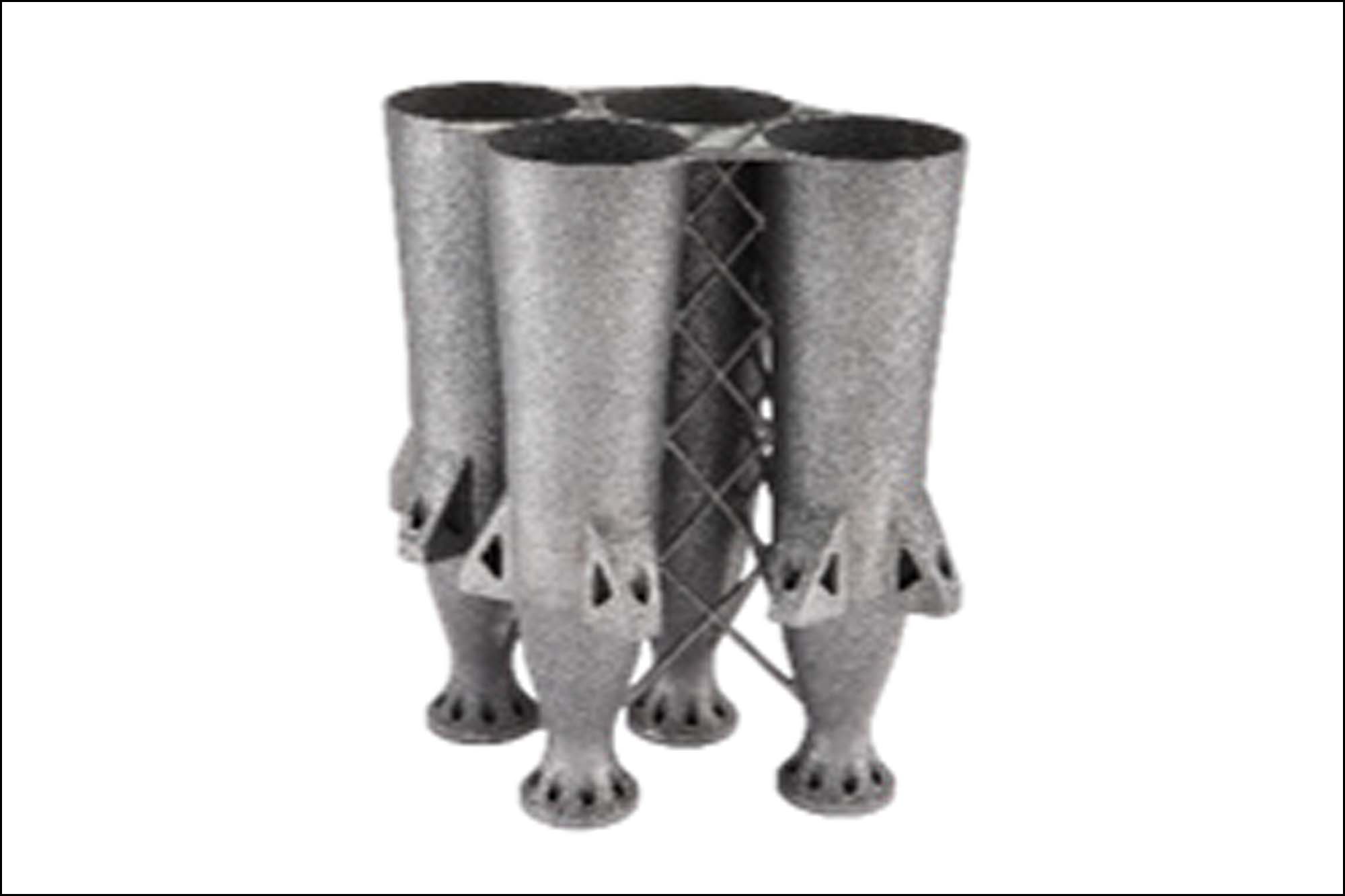
Wipro 3D’s end-to-end AM adoption framework is built around a structured, phased approach. It begins with feasibility and application assessment, identifying components that offer the highest value from AM. This is followed by design optimisation using advanced tools such as topology optimisation and generative design. Once a part is redesigned, it undergoes process development, building strategy formulation and material selection. After manufacturing, parts are validated for compliance and reliability through non-destructive and destructive testing, which is critical in regulated industries such as aerospace and defence.
Current trends in additive manufacturing that are shaping the future of industrial production include significant hardware improvements, which are making machines larger, faster, and more precise. The automation of processes from build preparation to post-processing is also gaining momentum, improving consistency, reducing human error, and driving scalability. Other impactful trends include the integration of AM into digital manufacturing ecosystems and the use of AI and machine learning for process optimisation and predictive maintenance.
Wipro 3D takes a rigorous approach to material qualification and process standardisation, especially for mission-critical applications. The company has significant experience in adapting non-native metal alloys and novel polymers into additive manufacturing, some of which have been certified or approved for military use. This involves comprehensive material characterisation, including mechanical, fatigue, and metallurgical testing, alongside the development of process parameters specific to each material and machine setup. These practices ensure consistent quality and performance across production batches.Sustainability and lightweighting continue to be key drivers for AM adoption. Wipro 3D supports these goals through advanced design techniques of topology optimisation, which minimises material usage while maintaining functional integrity. This reduces part weight and contributes to energy efficiency in sectors such as aerospace and oil & gas.
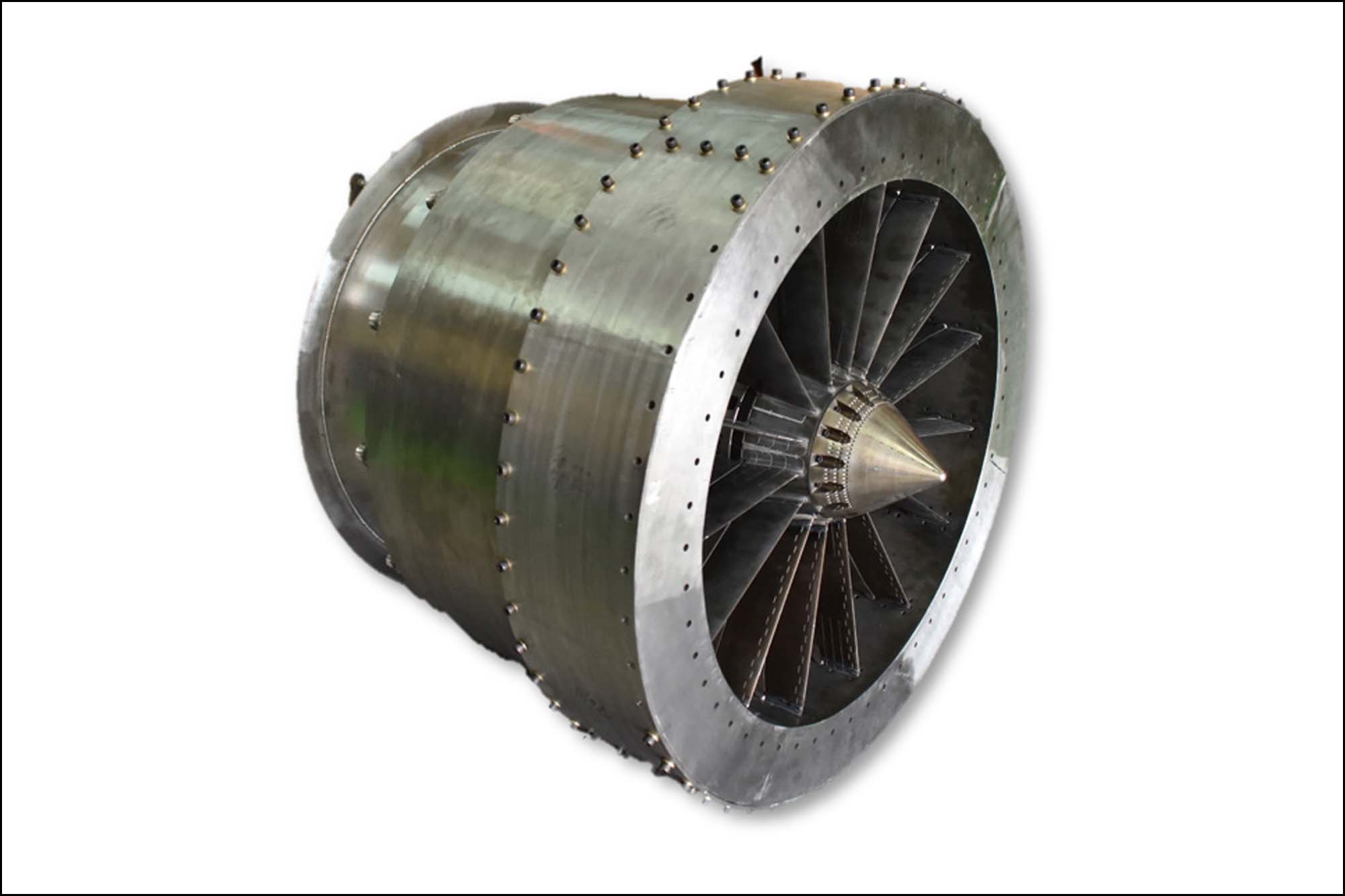
One of the biggest challenges in convincing traditional manufacturers to shift to additive manufacturing is overcoming scepticism regarding cost, reliability, and scalability. Wipro 3D addresses these concerns by demonstrating tangible value through pilot projects, business case modelling, and real-world success stories. Through tailored roadmaps and skill-building programs, Wipro 3D helps manufacturers make informed, confident transitions into additive manufacturing.
Cookie Consent
We use cookies to personalize your experience. By continuing to visit this website you agree to our Terms & Conditions, Privacy Policy and Cookie Policy.