Zero waste Automaking
By Staff Report July 1, 2025 6:31 pm IST
The automotive industry is accelerating towards cleaner mobility, with manufacturers facing a new imperative: eliminating waste across the entire value chain. From raw material sourcing to component production and end-of-life recycling, zero-waste manufacturing is becoming a crucial benchmark for sustainable progress. Drawing on insights from sustainability experts and industry leaders, OEM Update’s July cover story explores how automotive OEMs and Tier-1 suppliers can adopt circular economy principles and optimise production processes to minimise material waste.
Electric mobility conversations often focus on “electric vehicle emissions” and “charging challenges,” but a critical issue in the auto industry is waste. We should view waste as a starting point for innovation rather than an endpoint. Achieving zero waste requires a complete redesign of systems to ensure that all materials, from plastics to metals, are reused, recycled, or composted, thereby minimising landfill disposal.
In India, the fourth-largest auto market, sustainability is essential for long-term competitiveness. Although the government’s scrappage policy is a positive move, over 90% remains unorganised. High costs of recycled materials and inconsistent regulations present additional challenges. Success stories, such as Tata Motors’ and Mahindra’s zero-waste facilities, are limited by design constraints that hinder easy dismantling and remanufacturing.
Supportive initiatives, such as the Production-Linked Incentive scheme, can help cultivate a circular auto economy, targeting a $15–16 billion market by 2030 and creating green jobs. Vinkesh Gulati from the Automotive Skills Development Council emphasises the need for redesign and collaboration to achieve zero waste.
While India is advancing from awareness to execution, evolving older systems will take time. All automotive manufacturers are now focused on end-to-end strategies for net-zero emissions. The industry accounts for about 7.1% of India’s GDP and has over 30,000 dealerships nationwide. Educating dealers on sustainability varies by region, with urban areas generally more aware.
In terms of the glass industry, recycling options in lower-tier towns are lacking, although support exists in tier-one cities. Organisations like SIAM and ACMA now assess environmental impacts, a notable evolution from previous practices. While solar energy was once seen as the sole solution, it’s clear that many more possibilities exist, and the journey toward sustainable practices continues.
Challenges in embedding a zero-waste culture
One challenge in manufacturing is the traditional mindset that accepts waste generation as a norm in production processes. Manohar Sethpalani, Head Quality & EHS- Manufacturing, Varroc Engineering, shares, “It is essential to challenge this mindset when developing new products or processes, and this shift in perspective must be embraced by everyone involved.”
Another challenge is that recycled materials often cost more than their original counterparts. However, new materials and innovative solutions are emerging to address this issue. Technologies such as chemical recycling, bio-based composites, and closed-loop material recovery are showing promise in reducing costs and improving performance.
In the automotive industry, a specific challenge is ensuring that parts have the same longevity as the vehicle itself to minimise waste. Achieving this goal requires advancements in both technology and mindset.
Practices such as reverse logistics and bin reuse have become standard in the supply chain. A new trend emerging is the effort to eliminate packaging. However, the biggest challenge remains in the area of dedicated vehicle components. The parts that make up a vehicle generally have a lifespan similar to that of the vehicle itself. This alignment in longevity leads to reduced waste generation within the ecosystem. Implementing this concept in reality presents two main challenges: one is technological, and the other is related to mindset.
Mr Sethpalani adds that Tier 1 suppliers have their challenges. He shares, “We have multiple plants across the country that produce electrical, electronic, metallic, and polymer products. When we consider waste, particularly waste circularity and reduction, we can see multiple benefits. The concept of preventing waste generation carries both economic and environmental advantages. As we embark on this journey, we find that both aspects can go hand in hand. Focusing on waste reduction or circularity does not necessarily harm operational margins; instead, we can often achieve an optimised balance between both.
For example, by reducing the number of setups in our processes, we can decrease scrap and waste. We also deal with something called “end pieces” (typically off-cuts or unused remnants in production). By optimising the entire setup cycle, we can minimise waste, enhance operational efficiency, and make a positive contribution to the environment. There are numerous ways to reuse the waste we generate, and it involves thinking beyond our organisation. We can identify other organisations that could use our waste as raw material or input.
Overall, in the automotive industry, both OEMs and tier-one suppliers have reached a point where sufficient data is available. Many companies have devised plans for their journey over the next five to ten years. While challenges remain, they are not insurmountable. Most companies are now assessing their current positions and developing journey plans for the next five to ten years. Many aspects of sustainability have been largely addressed, and while challenges still exist, they are no longer foundational hurdles in this regard.
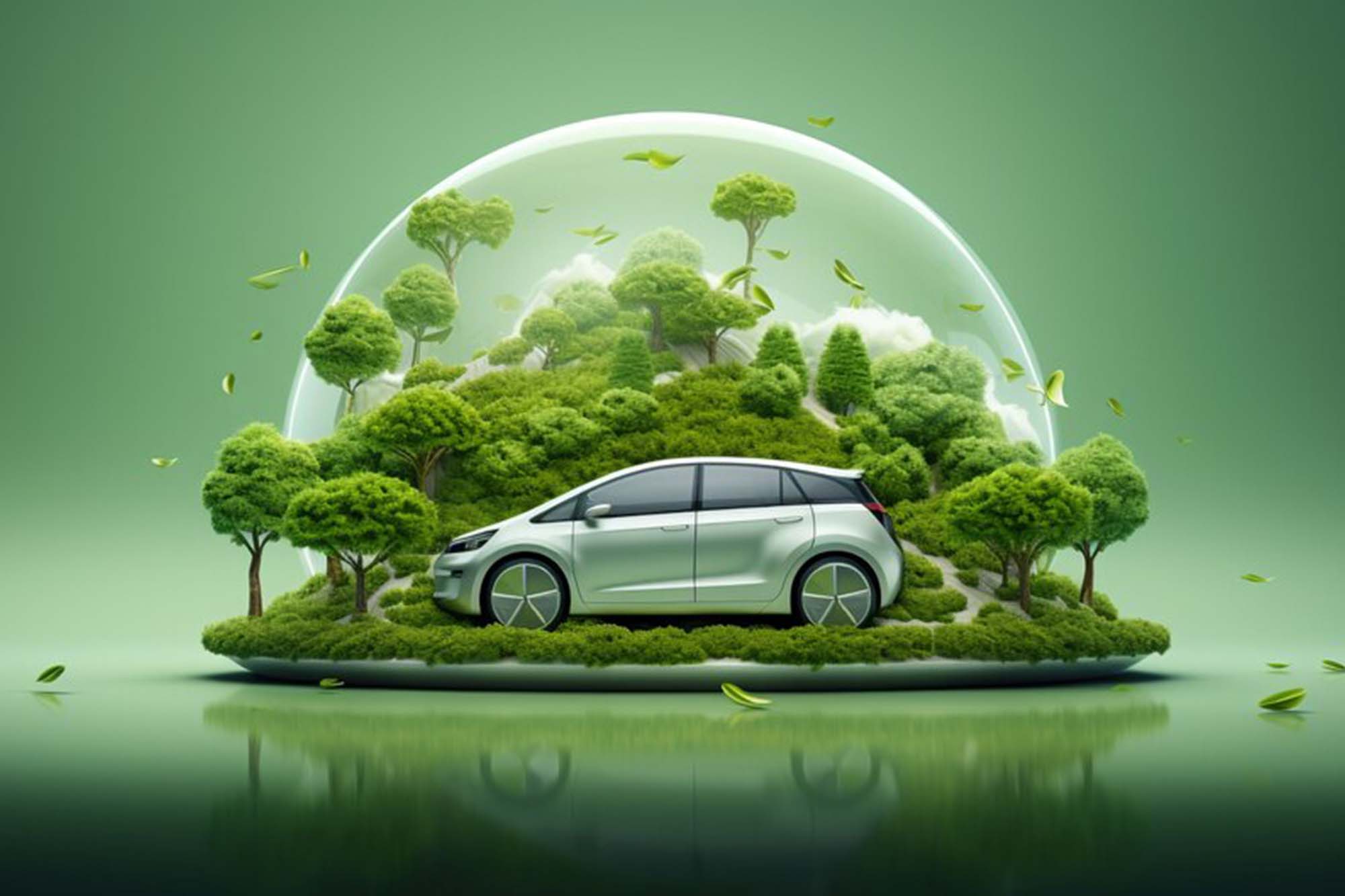
Framework for OEMs
The Big Four companies, along with a few others, are currently working to reduce waste in their manufacturing units. However, implementation comes with costs, particularly since recyclable parts are often more expensive than the main components. While the theory and research are well-established, the implementation is not yet at the optimal stage. Some OEMs are stepping up as pioneers in this field.
We need dedicated teams within each OEM to explore opportunities for reducing waste. In Delhi, we observe a significant number of landfills, so why can’t we utilise these materials? Some startups are making strides by compressing plastic bottles to create useful products. While the idea of going plastic-free sounds appealing, we must consider whether we can deliver a satisfactory customer experience without using plastic bottles.
Many dealers are making an effort; for example, several provide saplings as part of vehicle deliveries. We are in the race to improve and make progress, but it will still take time. Any plans we develop from scratch today should focus on achieving greater efficiency, as the existing systems will require time to adapt and evolve.
Startup Perspective
While describing the perspective of a startup, Bharat Pritmani, Co-Founder of Xero EV, says that when a product is an idea, the first steps involve checking the availability of materials, pricing, usability, lifespan, and whether it meets specific requirements. Often, considerations of circularity and end-of-life are neglected. He adds, “At the inception of Xero, we aimed to address a pressing global environmental need. Initially, we explored hydrogen as a solution. However, after assessing the situation, we realised that the ecosystem wasn’t prepared for it, prompting us to shift our focus to electric vehicles, where the ecosystem was developing more robustly. It is challenging to advance a technology that faces ecosystem-related hurdles. Therefore, we decided that electric would be our primary focus.”
Recycling
Collaboration is key to establishing partnerships with the right recyclers, ensuring that materials return to manufacturers. In the battery industry, full circularity is not yet achieved because recycled materials aren’t consistently being sent back to cell manufacturers. However, Siddharth Mohantty, Co-Founder, thinks that with the emergence of new gigafactories in India and globally, there will be a growing demand for domestically sourced recycled materials like cobalt sulfate, lithium carbonate, and nickel sulfate.
In the case of metals such as aluminium and copper, recycled materials are more effectively reintegrated into the production of automotive and electrical components. Achieving a closed-loop system for lithium-ion batteries will likely take an additional four to five years, depending on advancements in recycling technology and the development of robust reverse logistics.
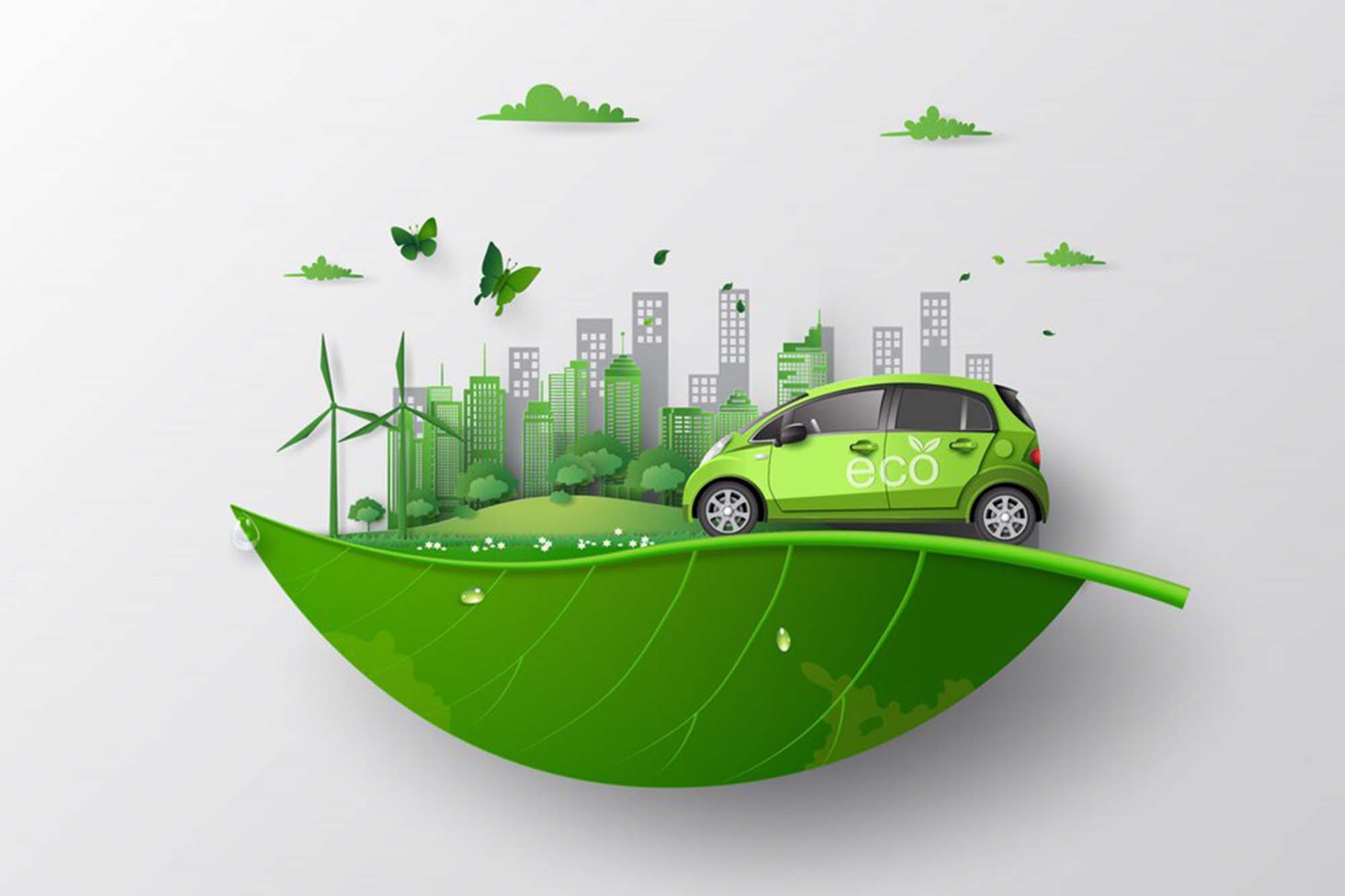
Role of Academics
Education should help students adopt a mindset: what we produce must be ready for use, and we should avoid wasting natural resources in the manufacturing process. Pratik Pancholi, Robotics Trainer at Tata Indian Institute of Skills, says, “We begin by training individuals to use the correct tools. For instance, in battery pack assembly, suppliers often encounter issues where cells are wasted due to incorrect assembly techniques or improper fitting. We emphasise this mindset in our training by teaching the importance of using the right tools for the right job.”
There are growing career opportunities for students in the battery ecosystem, especially in research and development. Those with experience in battery design or recycling can pursue postgraduate programs and MBAs focused on energy systems, electric mobility, and battery technology. Newcomers to the electric vehicle (EV) or recycling industries need to acquire skills in mechanical design or battery technology, as approximately 30% to 40% of an EV’s cost is attributed to its battery. Emerging technologies, such as lithium iron phosphate (LFP) and sodium-ion batteries, aim to reduce these costs. Prioritising training that addresses current industry needs is crucial for success in this field.
Cookie Consent
We use cookies to personalize your experience. By continuing to visit this website you agree to our Terms & Conditions, Privacy Policy and Cookie Policy.