Manufacturing scale-up with Industry 4.0 technologies
By OEM Update Editorial June 5, 2024 5:54 pm IST
Addverb, under the leadership of Nitin Rawat, General Manager of Production, utilises automation technologies, strategic partnerships, and continuous learning to enhance efficiency, scalability, and sustainability in manufacturing operations.
How do technologies like IIoT, AI, and ML enable manufacturers to scale up production?
Scaling up production is crucial in the competitive manufacturing landscape. This requires a strategic approach that incorporates technologies such as the Industrial Internet of Things (IIoT), machine learning (ML), and artificial intelligence (AI) to automate operations, optimize workflows, and extract valuable insights from data. The IIoT enables real-time data analysis, while AI and ML algorithms identify patterns and optimize production schedules, leading to increased productivity and reduced downtime.
Automation technologies that join the ensemble include autonomous systems and robotic process automation (RPA), which precisely handle repetitive operations. Regarding jobs like welding, industrial robots excel at increasing output and reducing errors. Moreover, cutting expenses, Automated Material Handling Systems (AMHS) offer logistical help.
Moreover, the vast amount of data generated holds the key to further optimization. Big data analytics tools analyse data to identify inefficiencies and suggest improvements, while Digital Twin technology allows for simulations before real-world implementation. Through strategic implementation and incorporation of some of these technologies, manufacturers can achieve great results from their processes while reducing the cost of production. This technology-driven approach creates a platform for sustainable growth and long-term success.
What strategies can be employed to ensure optimal utilisation of robotic systems?
Collaborative robotics (cobots) with sophisticated sensors and vision systems must be integrated if advanced robotics is to be used for accurate assembly and increased productivity. These cobots can assist human operators in assembly activities, improving accuracy and productivity.
Integration with AI algorithms allows for adaptive control and error detection, ensuring accurate assembly processes. Additionally, investing in robotic training programs for employees ensures optimal utilisation of robotic capabilities and boosts overall productivity. Implementing preventive maintenance schedules and continuous monitoring of robotic systems also improve reliability and uptime, further enhancing productivity and assembly accuracy. Manufacturers can achieve perfect assembly and enhanced productivity by combining modern robotics with smart training and maintenance procedures.
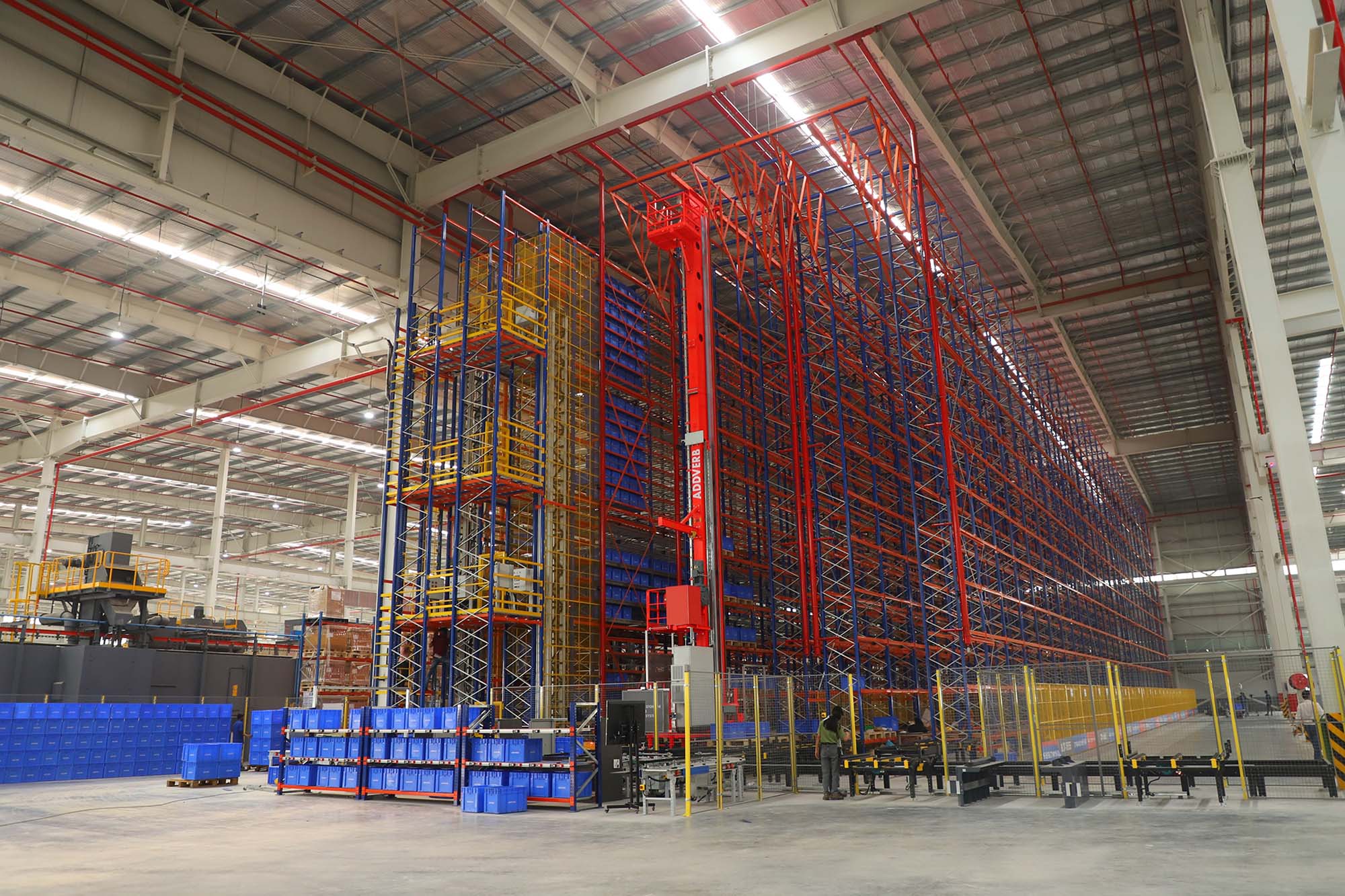
What benefits do WMS software and IoT sensors bring in terms of productivity and ensuring scalability?
Industry 4.0 technologies are driving substantial breakthroughs in our organisation’s manufacturing operations. We are utilising modern WMS software, IoT sensors for predictive maintenance, collaborative robots for flexible manufacturing, and AI-driven algorithms for process optimisation.
These developments transform how we manufacture goods, increasing productivity, quality, and adaptability to changing consumer needs. IoT sensors enable proactive maintenance to avoid downtime and save expenses by providing real-time data on equipment health. Collaborative robots increase flexibility by collaborating with human operators, optimising workflows, and enhancing ergonomics. Artificial intelligence (AI)-powered algorithms evaluate data to maximise efficiency, reduce waste, and improve production schedules. These developments improve our manufacturing capacities and guarantee market competitiveness, scalability, and agility.
Artificial intelligence (AI) algorithms are widely used in the healthcare industry for tasks including predictive modelling, clinical note natural language processing, and medical imaging analysis. Advanced WMS software integrates with various technologies, such as barcode scanners, RFID tags, and automated conveyor systems, to streamline warehouse operations. WMS enables real-time tracking of inventory, efficient order fulfilment, and better utilisation of warehouse space.
How does your company overcome manufacturing challenges to scale up processes?Our approach to overcoming manufacturing challenges and scaling up processes is not just about us, but about the power of collaboration. We centre on people development, strategic partnerships, and continual innovation to efficiently address manufacturing constraints and scale up processes. We make research and development investments to provide innovative solutions that meet the industry’s demands. Through collaboration with technology suppliers and industry leaders, we can access new technologies and best practices, which speed up process improvements and scalability. This collaborative approach empowers us to drive sustainable growth and competitiveness in our industry.
We prioritise workforce training and upskilling to enhance skills, adaptability, and problem-solving capabilities. Additionally, we implement agile methodologies to quickly adapt to changing market dynamics and customer requirements, ensuring responsiveness and efficiency in scaling up processes. By leveraging innovation, collaboration, and talent development, we overcome manufacturing challenges and drive sustainable growth and competitiveness in our industry.
Addverb is a company that follows a customer-centric approach. It means that it focuses on understanding and addressing its customers’ unique needs and challenges. To achieve this, it actively seeks feedback and insights and tailors its solutions to meet and exceed customer expectations. We are flexible and responsive to adapt our strategies and offerings quickly to stay ahead of the competition and meet evolving customer needs.
Finally, we prioritise quality and reliability in our products and services. We ensure that customers receive robust, efficient, and dependable solutions by maintaining stringent quality standards and investing in rigorous testing and validation processes. This builds trust and loyalty among its customer base.
How does your company’s continuous learning and upskilling strategy inculcate empowerment through training programs?
Our strategy for creating a culture of continuous learning and upskilling workers is not just about improving our operations, but about investing in our most valuable asset-our people. We offer training programs focused on technical skills, soft skills, and industry trends to ensure ongoing learning and development. Mentorship programs pair experienced employees with newer hires to foster knowledge transfer and skill enhancement. Cross-functional collaboration encourages teamwork, innovation, and shared decision-making, empowering employees to contribute ideas and take ownership of projects. Additionally, we recognise and reward initiative, creativity, and problem-solving, creating a culture that values continuous improvement and encourages personal and professional growth. This strategy cultivates an agile, adaptive, and motivated workforce to excel, driving innovation, efficiency, and success in our organisation.
What is your perspective on the sustainability of scaling up operations without modifying the existing operational approach?
Scaling up without evolving operational approaches can be unsustainable in the long run. As businesses grow, they must adapt their strategies, processes, and technologies to meet emerging demands efficiently. Embracing innovation, optimising workflows, and leveraging scalable solutions are essential for sustainable growth and long-term success in today’s dynamic business environment. Evolving operational approaches involve continuous improvement, agility, and flexibility to respond to market changes and customer needs. It also requires investment in technology, talent development, and strategic partnerships to drive innovation, improve efficiency, and maintain competitiveness. By embracing change and adapting proactively, businesses can sustain growth, drive value creation, and achieve long-term viability in the market.
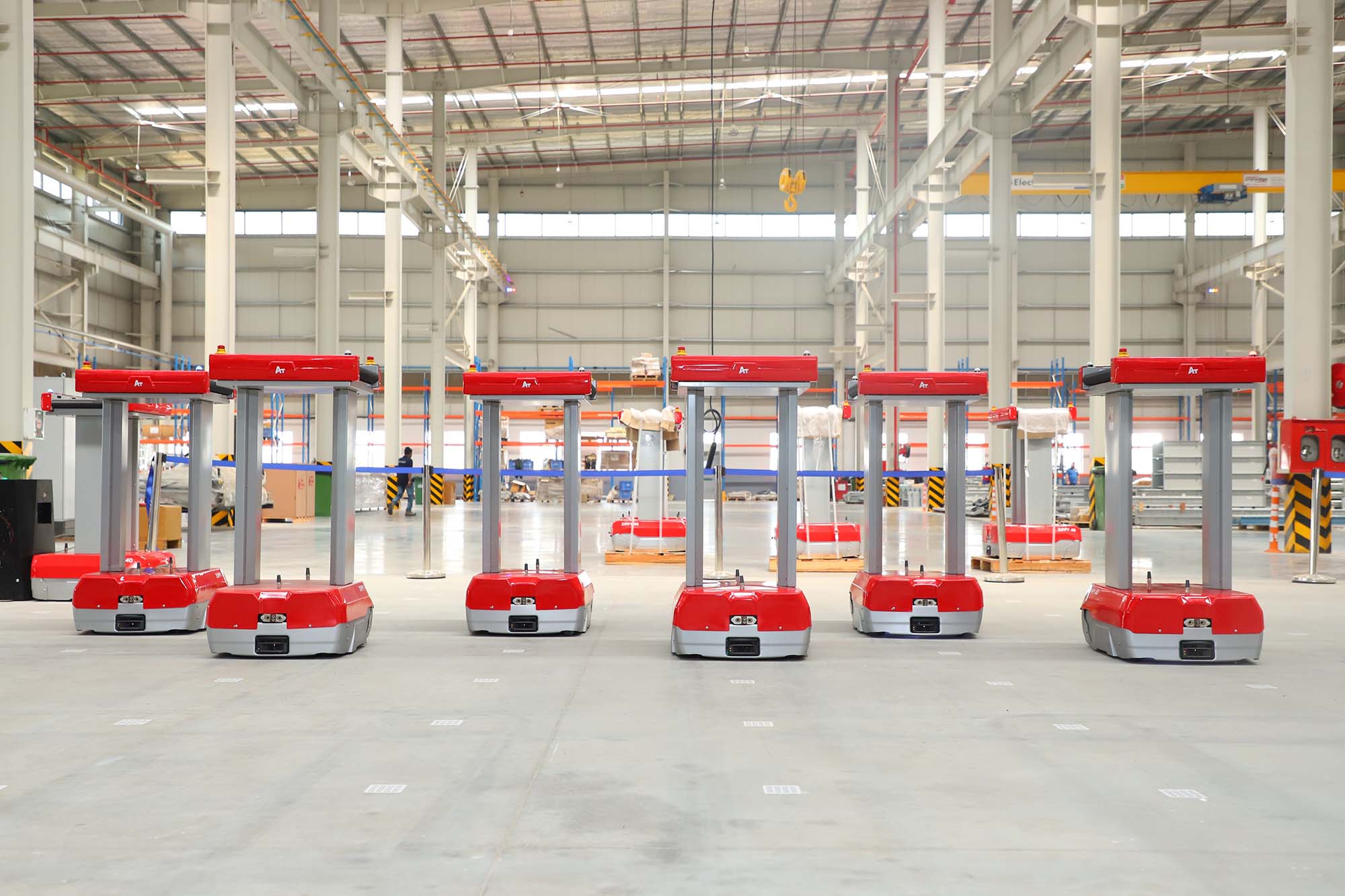
What are the benefits of the manufacturing-scaling Make in India initiative?
The Make in India initiative presents several advantages for scaling up manufacturing, including economic growth, job creation, and technology development. By promoting indigenous manufacturing, the initiative reduces imports, enhances self-reliance, and strengthens the domestic manufacturing ecosystem. It attracts foreign investment, technology collaboration, and industry expertise, boosting industrial capabilities and competitiveness. The initiative fosters innovation, entrepreneurship, and industry diversification, leading to product innovation, market expansion, and global competitiveness. Additionally, Make in India initiatives like infrastructure development, policy reforms, and skill development programs support manufacturing growth, job creation, and economic development across sectors. Overall, the Make in India initiative drives industrial growth, promotes manufacturing excellence and positions India as a global manufacturing hub.
Cookie Consent
We use cookies to personalize your experience. By continuing to visit this website you agree to our Terms & Conditions, Privacy Policy and Cookie Policy.