Grinding requires smart automation
By OEM Update Editorial March 2, 2023 1:49 pm IST
Faster, more accurate, and more cost-efficient machining is only one of the advantages of automating grinding processes. STUDER is therefore one of the technology leaders in this field.
“There are still a lot of prejudices about automation in grinding,” says Daniel Schafroth, Systems Division Manager at STUDER. There are frequent concerns that people or jobs could become redundant. At STUDER, the opposite holds true: Automation should enable the human operators to do their work more easily, efficiently, and safely. Additionally, the special requirementof grinding necessitates that automation is used verywisely and selectivelynot every solution used in the industry is suitable for this. But what are the important factors?
“For grinding, it is particularly important that processes are performed repeatedly in the same way, with high precision and reliability. One example is clamping workpieces and aligning them correctly with micrometer accuracy,” explains Schafroth. Automatic solutions for multi-machine operation can greatly relieve the workload of the operators. They then only have to fill magazines and no longer need to laboriously load each machine. However, grinding fundamentally requires the operators to have a high level of competence, and automation should not be something that hinders them,” says Schafroth: “Automation only makes sense where the operator doesn’t have to have a decisive influence on the process.”
Small companies profit from easyLoad
Automation can be a real game changer for grinding companies—regardless of whether it is a small business or a large company with several systems. “Where grinding machines are concerned, automation pays off for all sizes of companies,” emphasizes Schafroth. A small workshop with only a few employees can fill the grinding machine in the morning. Later, it can work autonomously for extended periods while the employees take care of other things, such as writing quotations. The easyLoad loading system for external and universal cylindrical grinding machines (S31, S33, S22,and S41) which offers excellent value for money. It includes integration in the machine control and is explicitly also aimed at small companies.
easyLoad is suitable for use as a gantry loading system for shaft parts with a workpiece length of up to 300 mm (11.8“), a diameter of up to 30 mm (1.18“), and interfering contour diameters of max. 50 mm (1.97”). The adjustable synchronized conveyor allows autonomous processing of max. 50 workpieces. The standard gripper is designed for individual parts, the V-gripper for two parts, and the heavy-duty gripper for workpieces that weigh more than five kilograms (11 lbs.). The changeover time is only around six seconds. This enables the machine to run autonomously for half an hour or longer with ease.
ecoLoad and uniLoad increase production
STUDER has also developed optimal automation solutions for larger-volume series production. “Small companies mainly benefit from the universal and flexible systems, whereas speed and precision are the important factors in the production of large quantities,” explains Schafroth. Here, good automation concepts can produce a large number of high-quality workpieces and make the most of every second. The ecoLoad for the STUDER S22 production platform is an automatic loading system for series production using high-speed grinding, production-oriented cylindrical grinding, as well as form and thread grinding.
ecoLoad can load workpieces with a diameter of up to 50 mm (1.97”) and a length of 250 mm (9.85”). This is either done using a carousel magazine or an insertion prism, which can also be used as the interface for standalone tool magazines. The programming is already integrated into the grinding machine control. This ensures short retooling times.
The uniLoad automatic loading system also makes it possible for operators of the STUDER S31 and S33 external cylindrical grinding machines to significantly increase productivity without any loss of quality.
The system docks to the machine from the left. With a prismatic conveyor and all racks at full capacity, it can perform automatic processing for around an hour. It is suitable for workpieces with a length of up to 350 mm (13.8”) and 100 mm (3.94”) diameter and thus covers a large range of the parts normally produced on these machines.
Solutions for applications with limited space are another important trend in the automation of grinding. “In modern production halls, it is of particular importance to make efficient use of the space,” says Schafroth. This is another topic where STUDER is a trailblazer, for example with the smartLoad for the S11, a production cylindrical grinding machine for small workpieces which has a footprint of only 1.8 square meters (19.4 sq. ft). The smartLoad unit is also compact and can feed in workpieces from outside the machine, using either a conveyor or a swiveling unit, as well as clamp them and place them back after the machining. Thanks to the wide variety of configuration options, numerous applications are possible, for both small and large-volume series.
In the past, radius internal cylindrical grinding machines, which are used in the manufacturing of drawing dies, for example, have been particularly difficult to automate, due to the limited space available. One reason for this is the restrictedenclosure geometry resulting from the high workhead. STUDER has now developed an optimal solution for this as well: roboLoad. This external loader for the S121, S131, and S141 is designed as a gripper arm with quick-change jaws and has a lot of space for workpieces on six trays (each 1080 x 320 mm (42,5 “ x 12.6”)). At 1.50 m (59”), the system is only half the width of the machine itself.
“With the robot arm outside the machine, we gain a lot more freedom, thanks to the rotation axis, and the roboLoad can get in for loading and unloading without having a direct pathavailable,” says Schafroth. Until now, automation solutions for grinding were largely based on linear technology such as beams and slides. However, at the moment the roboLoad is not primarily intended for large series production, but more for automated production during night shifts or extended breaks. But Schafroth is sure that the trend toward using robotic arms in grinding will persist. “Neither our customers nor we want to relinquish this new freedom.”
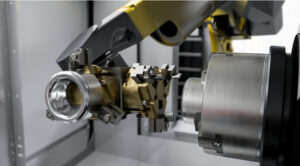
Automation is digital as well
This freedom includes easy and intuitive operation, a special USP of roboLoad and the other STUDER concepts. “The grinding machine operators do not need any programming skills to perform the setup; it can be done easily and quickly within a matter of minutes,” says Schafroth. For him, automation in grinding means more than just physical machine support. It is equally important to have digital assistance, such as that offered by the STUDER grinding software and in particular C.O.R.E., the revolutionary new cross-brand hardware and software architecture of the UNITED GRINDING Group.
On the large C.O.R.E. touch display with intuitive icons, the operators can quickly find what they need and important information regarding the machining process is displayed. RFID access chips can be used to let the machine only display the options and information for which the individual users are qualified. “This prevents unqualified employees from making changes that could cause an error or a crash,” explains Schafroth. With applications of UNITED GRINDING Digital Solutions™, efficient remote monitoring of the machines is possible even today, and in the future machines will monitor themselves for optimal functioning and proactively provide information on required maintenance measures.
The possibilities for automation in grinding are therefore very diverse and offer large advantages on different levels. However, as Schafroth emphasizes, the focus must always remain on people. “Something that is frequently overlooked regarding this topic is that automation also protects the safety and health of the workers.” Robots can not only help with lifting heavy loads and performing repetitive, boring tasks but also handle a wide range of different materials without problems. This makes the workplace a lot safer and more comfortable. Schafroth says that he is happy that the prejudices regarding the topic are decreasing and that automation solutions are becoming more and more frequent in grinding, and adds: “Because the best machine technology in the world is useless if it is not accepted by the people.”
Advantages at a glance:
- Automation in grinding protects the health of the operators and makes their workplaces safer and more comfortable.
- In small grinding companies with few employees, automation gives the staff more time for other tasks.
- In large-series production and mass production, grinding machines with automation can process large quantities very quickly, and with consistent quality.
- Smart, network-capable software and digital assistance systems form part of automationecause they make the work easier and faster for the operators and increase the quality.
- STUDER has developed optimal automation solutions for a variety of applications: easyLoad (S31, S33, S22, and S41), ecoLoad (S22), smartLoad (S11), uniLoad (S31 and S33), as well as roboLoad (S121 Radius, S131 Radius, S141 Radius).
Cookie Consent
We use cookies to personalize your experience. By continuing to visit this website you agree to our Terms & Conditions, Privacy Policy and Cookie Policy.