SmartJet for environmentally profitable cooling
By OEM Update Editorial March 2, 2023 12:49 pm IST
More efficient, more sustainable, and with shorter tooling times: with the new SmartJet ® concept from STUDER, a new era dawns for cooling systems in grinding applications. Both the customers and the environment profit from this.
A large part of the power and water consumed during grinding processes is required for the cooling. In these times of increasing energy prices and sustainability commitments, it is all the more important that the technological development in this field keeps progressing. STUDER has now achieved a true breakthrough with its SmartJet® concept: An intelligent cooling concept based on high-tech, which saves a significant amount of energy and resources – and additionally even simplifies operation considerably.
“SmartJet® can reduce water consumption by 40 percent and energy consumption by 50 percent,” says Martin Habegger, who is in charge of the project at STUDER. Those are substantial savings. But how are they achieved? In short: By using a clever nozzle design and an optimized line system with the appropriate pump for the machine line. Additionally, there is sensor-supported, intelligent control software that can support the operators to a much greater extent than in the past. Until now, operators had to take care of the cooling for the grinding process themselves. This involves first and foremost the correct positioning of the nozzles and manual adjustment of the volume flow, so that the pump can convey the cooling lubricant to the location where the grinding takes place.
Fundamental principles developed in cooperation with ETH Zurich
Firstly, this costs a lot of time and secondly, mistakes can easily happen and lead to unnecessarily high consumption. Frequently, operators use much more cooling lubricant than necessary or do not align the nozzles optimally. This is bad both for efficiency and the environment. To change this, STUDER joined forces with ETH Zurich to develop the technological bases and then advanced the SmartJet® concept to market maturity. With it, the machine control can now provide significant assistance with the coolant supply – in practice, this makes grinding much easier, moreprecise,and more efficient.
And this is how it works: The key components of the system are a frequency-controlled pump, and a ram pressure measuring unit. The cooling lubricant flows through an optimized line system, from the tank via a manifold to the flow-optimized and adjustable nozzles at the grinding wheel. There, a sensor measures the pressure upstream of the manifold. Using numerous parameters, the software then calculates the best exit speed for the volume flow, regardless of whether roughing, fine grinding, or finishing is taking place. Astonishingly, despite the low energy consumption of the pump, high pressure and exit speedsare achieved. “The jet of coolant is highly precise, coherent, and reproducible. The SmartJet® sets new benchmarks for effectiveness, process reliability, and efficiency in the industry,” says Habegger. The smart system also solves the problem of the flow of air over the wheelsurface, which, in the case of customary flat nozzles, can affect the optimal cooling of the grinding wheel: The solution is specially timed interruptions of the coolant jetflow, combined withthe high exit velocitywhich breaks through the air barrier around the wheel without compromising the effective cooling.
3D-printed high-tech nozzles
The innovative 3D-printed nozzles produced by STUDER’s sister company IRPD in St. Gallen also contribute to making this intelligent coolant system possible. Inside the streamlined design, there are several channels positioned next to each other. They distribute the cooling lubricant evenly across the width. If necessary, the downstream manifold can hold several nozzles in a row. The system has been designed as a modular solution with a quick coupler system, which makes it possible to recombine individual components in no time at all. It is always possible to adapt the nozzles individually to fulfill the needs of the customers, for example, the size of the nozzle cross-section. “As a machine manufacturer, we were able to plan and integrate the entire coolant system from start to finish, as well as match all components with each other and optimize them,” says Habegger. This is a great advantage over companies that only develop nozzles, for example. “Because the nozzles alone are not smart. It’s the entire concept.”
Another aspect with which the SmartJet® makes life a lot easier for people who need to do grinding work is the way the coolant supply is digitally integrated into the machine as an assistance system. The concept will already be part of the standard scope of delivery of the S36 cylindrical grinding machine, which is equipped with the cross-brand hardware and software architecture of UNITED GRINDING: C.O.R.E. On the large, intuitive touch display, the setup wizard helps to configure the nozzles for each workpiece optimally,and all relevant information is displayed. The grinding machine operator can choose between automatic or manual nozzle adjustment. And of course,the settings for different workpieces can be saved and are immediately available agan for the next use.
A particularly annoying problem that many grinding companies face is a thing of the past with the SmartJet®, explains Habegger. “After the grinding operation, cooling lubricant continues to drip onto the grinding wheel for a while, which can lead to an unbalanced wheelover time.” Some customary nozzles can be bent away to prevent this. But then they lose their optimal positioning and have to be manually aligned again prior to the next machining operation, which costs a lot of time. “Now grinding machine operators can simply move the nozzles a few millimeters away from the grinding wheel with the software control and later return it to its position with high accuracy.” This is only one example of how SmartJet® makes the daily grinding work easier with machine support and even increases the quality of the process.
The only question that remains: What is next for the SmartJet®? “We made the S36 the first machine to have it as standard equipment, because it is a high-performance production machine with a wide grinding wheel of 125 millimeters, which means that high-precision, efficient cooling can lead to particularly high savings,” says Habegger. The S36 has been specially designed for the volume production of precision workpieces. Additionally, some STUDER customers with other machine types have already had SmartJet® installed upon request. But within the current year, the intelligent coolant system is scheduled to become standard on the S31, S33, and S41 as well. “It is time for even more customers to profit from the advantages of the SmartJet®,” says Habegger. After all, it saves them costs, increases the quality, and sets new benchmarks for sustainability.
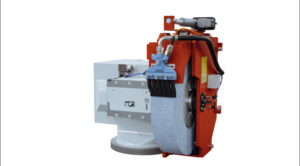
THE ADVANTAGES AT A GLANCE
- Optimized coolant supply
- Operator-independent, reproducible results
- Adjustments through themachine control
- High grinding power
- High process reliability
- Shorter tooling times
- Up to 40 percent lower water consumption and 50 percent lower energy requirements.
Cookie Consent
We use cookies to personalize your experience. By continuing to visit this website you agree to our Terms & Conditions, Privacy Policy and Cookie Policy.