Optimising gearbox efficiency conserves energy and reduces carbon footprints
By Staff Report November 16, 2024 12:35 pm IST
Innovative research and development efforts are underway to explore new materials, designs, and engineering processes for developing power loss mitigation strategies. Mahendran M., Proprietor at NexGenGears, accentuates the importance of optimising transmission systems in industrial machinery and mobility.
The transmission system is crucial for industrial machinery and mobility, and power losses in gearbox systems can affect performance and efficiency. Integrating engineering expertise, advanced software tools, simulation techniques, and stringent manufacturing quality controls improved transmission system performance and time.
The gear design process involves several phases, including conceptual design and testing. It aims to optimise gear technology to create robust, reliable, and lightweight components that minimise energy loss, improve efficiency, and remain cost-effective. This process ensures that the final product meets performance, efficiency, and durability requirements.
Gear geometry calculations have significantly improved transmission error and loss understanding, including optimal tooth profile sizing, module selection, helix angle, centre distance, material selection, tooth contact, load distribution, and dynamic behaviour under operational conditions. The knowledge enables the implementation of effective power loss mitigation strategies, supported by innovative research and development efforts exploring new materials, designs, and engineering processes.
KISSsoft and ROMAX are software solutions that offer powerful modelling capabilities for complex gearbox designs, including spur, helical, bevel, and planetary gears. They enable precise analysis of gear efficiency under different loading scenarios. Other tools like Masta, FVA, GWJ, and Dontyne facilitate detailed analysis reports and 3D gear models.
Contemporary software’s advanced dynamic simulation capabilities empower engineers to assess gearbox performance under various loading conditions and speeds, identifying inefficiencies in real time. These platforms support comprehensive evaluations of power losses due to friction, backlash, and thermal effects, offering actionable insights for design improvement.
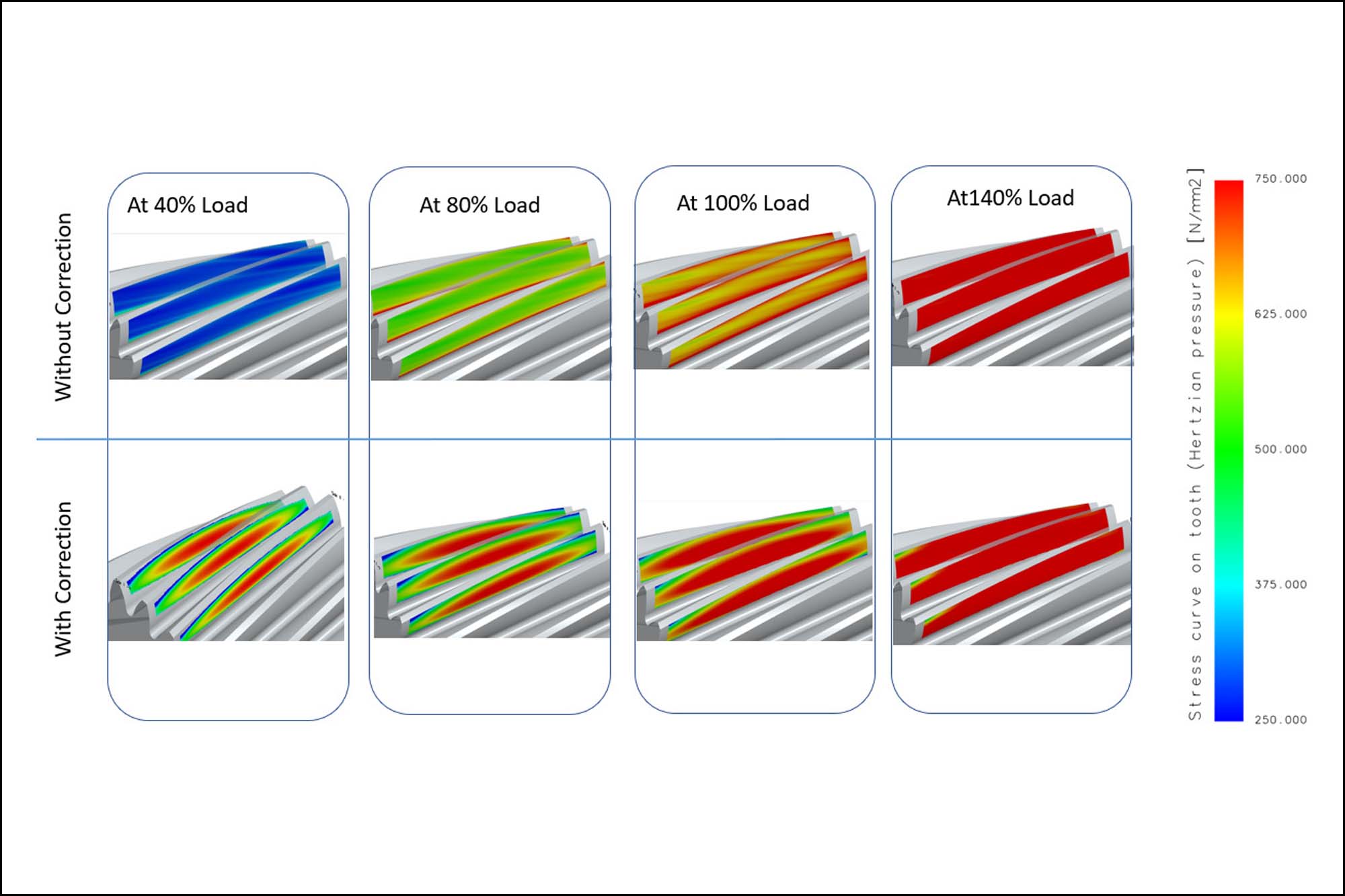
Gear design and analysis tools
Advanced analysis tools are vital in gear design, as they minimise transmission errors and enhance overall performance. CAD/CAM/CAE software, FEA, dynamic simulation tools, and system performance simulations evaluate gear interactions under varying loads and speeds, reducing backlash and improving mesh accuracy.
Shaft misalignment can result in uneven loading, increased friction, and premature wear, leading to power losses. Designs that enhance load distribution, such as wider gears or multi-stage configurations, can alleviate localised wear and reduce losses. Modern software allows for precise calculations and simulations of power losses due to friction, misalignment, and other factors, providing an overview of gearbox efficiency.
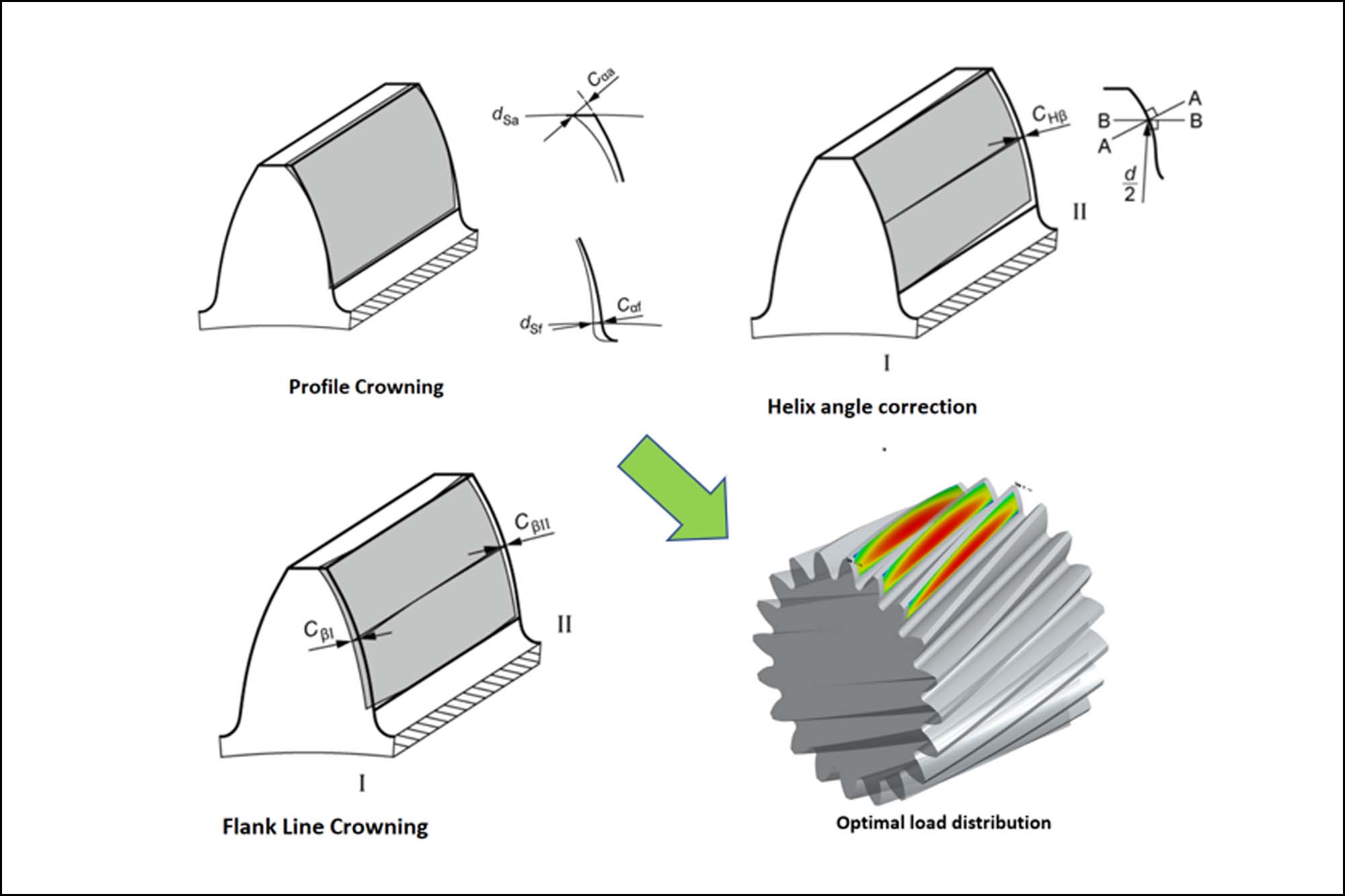
Gear teeth friction and energy loss
Gear tooth contact analysis identifies areas of improper engagement, allowing the redesign of tooth profiles to improve performance. Multi-body dynamics analyses the effects of vibrations and misalignments on transmission accuracy, guiding design modifications that align and stabilise. Optimal micro-geometry corrections can lead to uniform load distribution, diminishing localised stress and wear over time.Friction between gear teeth generates heat, resulting in energy loss, while poor heat dissipation can exacerbate temperature-related inefficiencies. Mass and rotational inertia can impede performance, increasing energy losses during acceleration and deceleration. Employing alloyed steels, surface treatments like case hardening, and lightweight materials from additive manufacturing can enhance durability and responsiveness, decreasing energy requirements.
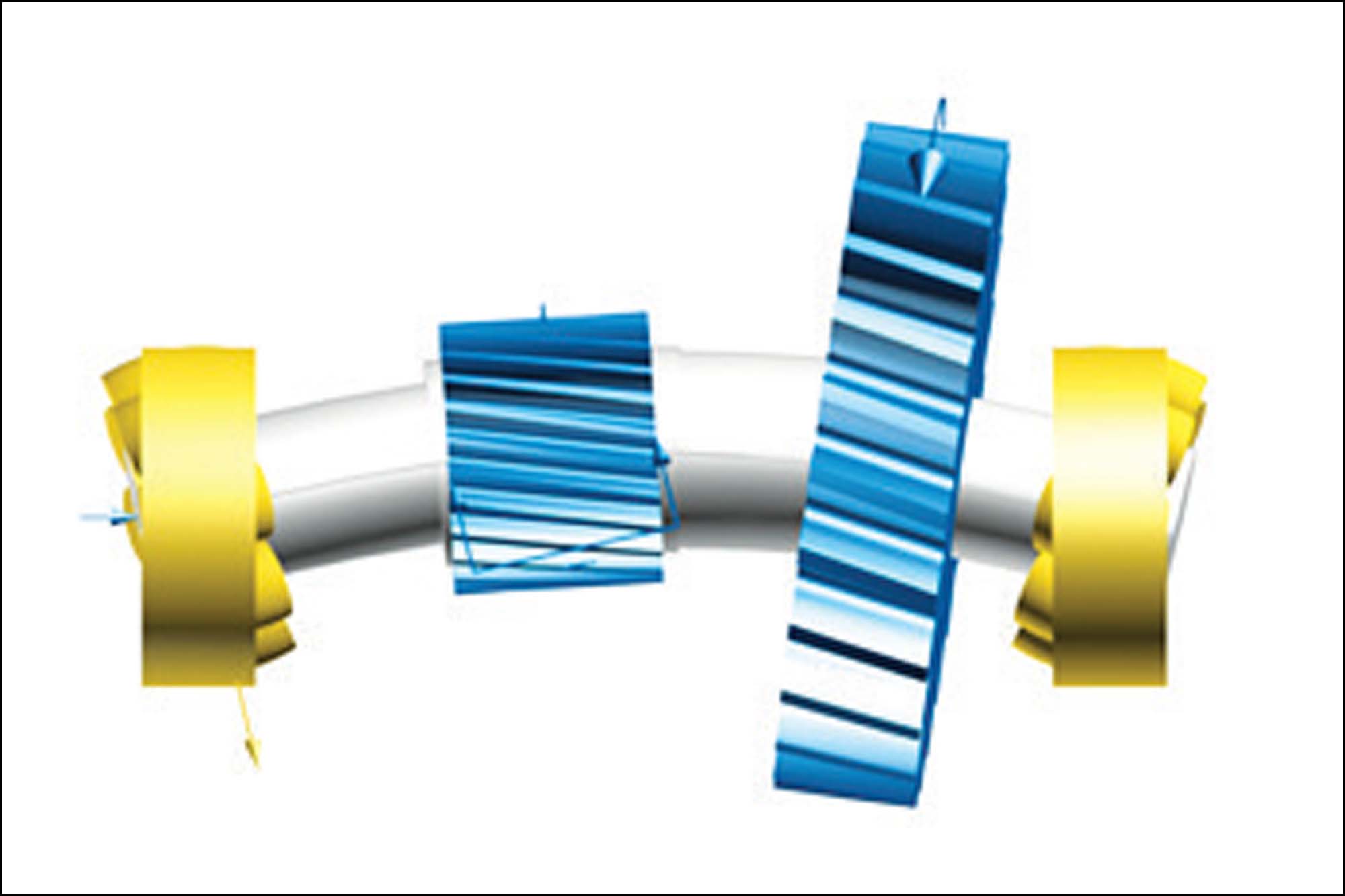
Optimisation algorithms automate design refinement, minimising transmission errors without extensive manual iterations. Virtual prototyping also reduces the need for physical prototypes for swift identification and resolution of potential issues.
Comprehensive load distribution analysis helps even load sharing, improving accuracy and reducing wear. Surface quality control ensures manufacturing tolerances are met, avoiding transmission errors. Strain gauges and vibration analyses detect operational strains for timely maintenance and design adjustments.
Lubrication in power transmission
Inadequate lubrication can increase friction and wear, leading to greater energy losses. Computational fluid dynamics (CFD) can improve lubrication systems for effective distribution and reduce friction and wear. Dynamic balancing and alignment tools minimise vibrations and energy losses.
Smart gearboxes with sensors facilitate real-time performance monitoring, generating temperature, vibration, and efficiency data to enable predictive maintenance. Applying big data and machine learning helps analyse operational patterns and guide design and operational improvements.
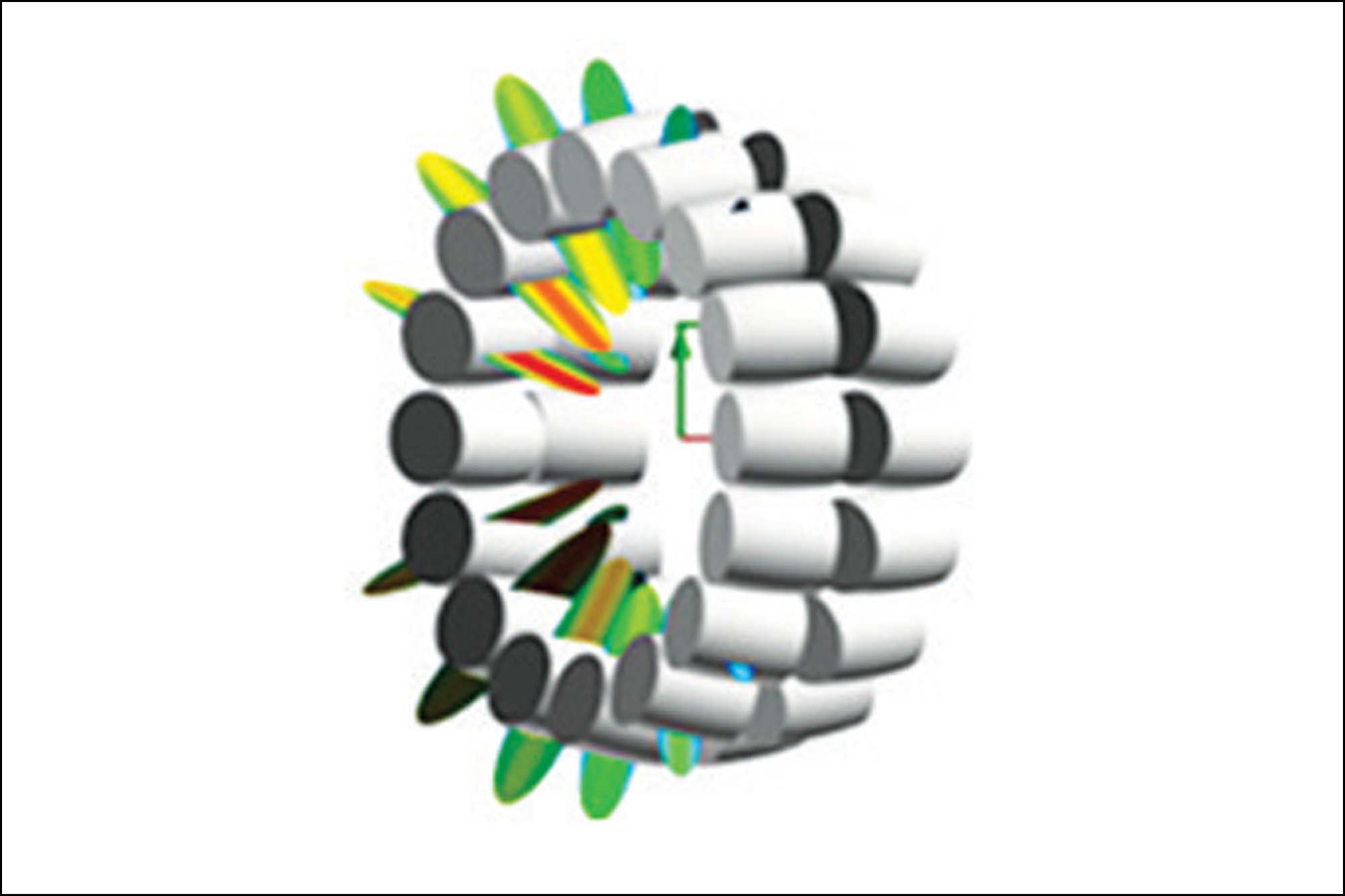
Machine learning and AI can predict transmission errors, inform design improvements, reduce risks, and improve power transmission accuracy. Optimal backlash estimation and precise assembly settings decrease energy losses, while smart technologies like CMS/SCADA are used for real-time performance optimisation.
These design advancements contribute to more efficient transmission systems, which reduce energy consumption and improve performance. Sustainability is a critical subject, and optimising gearbox efficiency conserves energy and reduces carbon footprints. Advanced software tools provide comprehensive support for analysing and gearbox efficiency, empowering engineers to make informed decisions that maximise performance. Digital twins strengthen gear performance simulation by improving designs before physical implementation, resulting in efficient gearboxes that are reliable, long-lasting, cost-effective, and sustainable.
Cookie Consent
We use cookies to personalize your experience. By continuing to visit this website you agree to our Terms & Conditions, Privacy Policy and Cookie Policy.